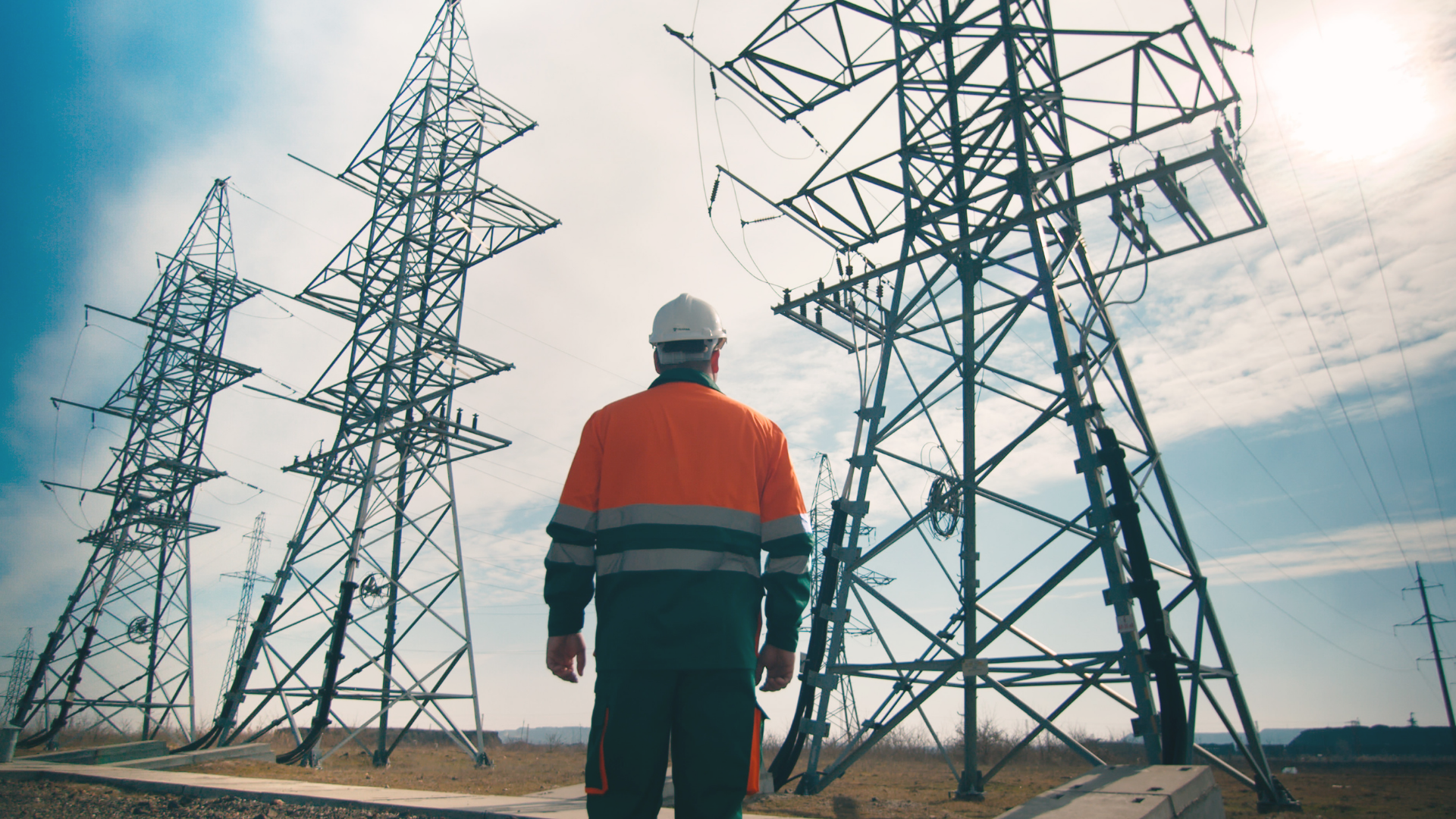
Even during the war, Ferrexpo continues to implement comprehensive energy saving programs
The Swiss iron ore company Ferrexpo, with assets in Ukraine, has long prioritized reducing energy consumption and saving all types of energy resources. Ferrexpo systematically implements projects aimed at improving energy efficiency. In 2015, the company started using sunflower husk as a partial replacement for natural gas. In five years of replacing gas with sunflower husks, Ferrexpo managed to reduce gas use by 25%.
During the full-scale war in Ukraine and Russia’s constant shelling of the energy infrastructure, this issue is even more pressing. Despite the difficult times, Ferrexpo, as a responsible business, continues to implement energy saving projects, which in addition to reducing costs and saving resources, also decrease its carbon footprint.
The company’s continuous improvement system
The energy efficiency program is part of Ferrexpo’s continuous improvement system. Despite the war in Ukraine and working at part-time capacity for more than a year, the company is still making progress with its ambitious decarbonization goals, and energy efficiency plays an important role in this direction and comprehensively complements the Ferrexpo decarbonization program.
Also, Ferrexpo is guided by the Carbon Zero strategy, which implies reduction of the carbon footprint to zero by 2050. The company’s experts estimate the capital investment required for decarbonization at $3.3 billion.
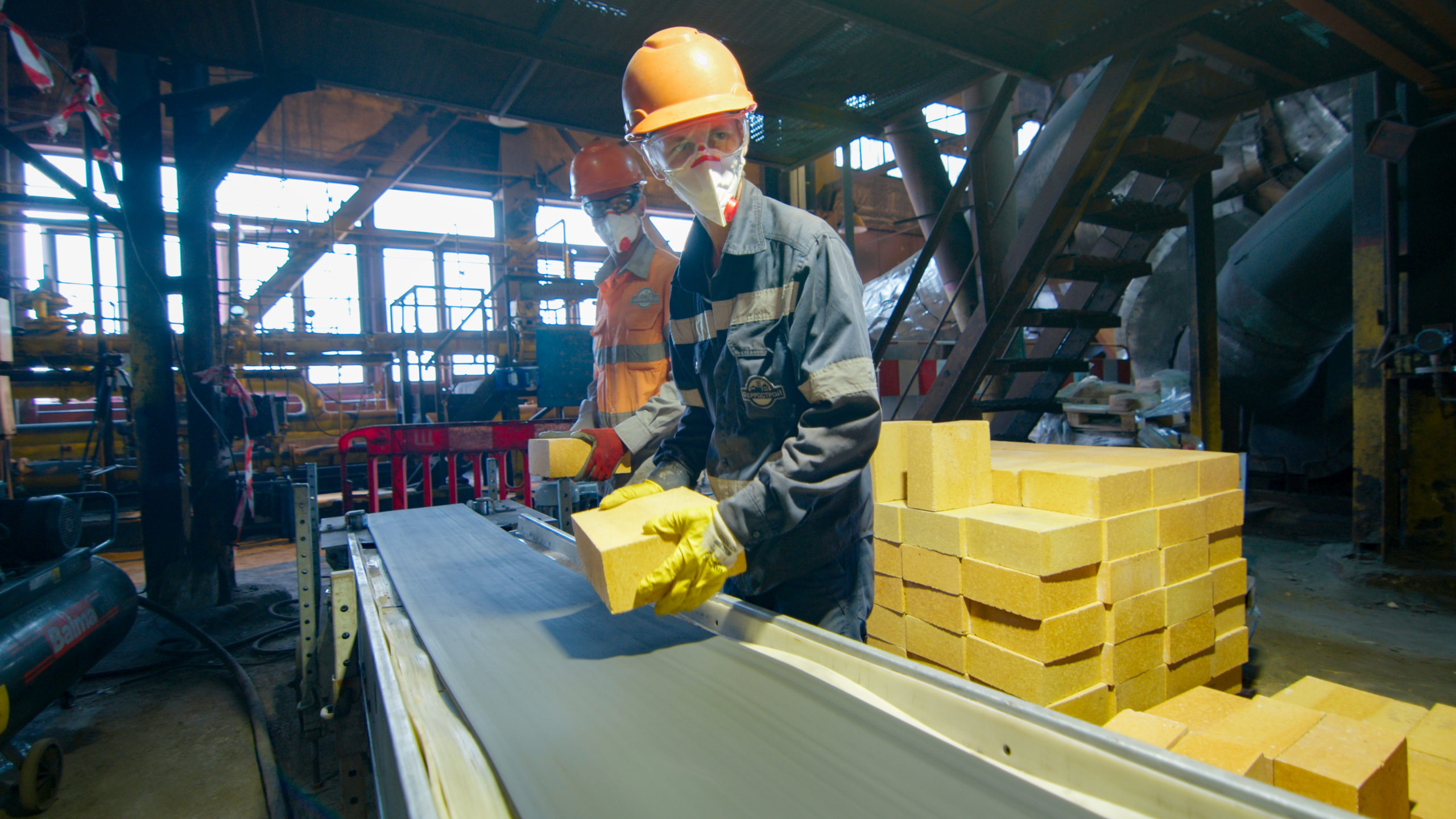
Ferrexpo
Lean and rational use of resources, modernization and replacement of energy-efficient equipment – collectively contribute to one of the company’s strategic goals – «FXPO 2050: CO2 = 0». The company has an energy saving policy, which fully complies with the requirements of the international standard ISO 50001:2018 «Energy Management Systems».
«We continue to implement energy efficiency projects. Of course, if it were not for the war, we would have been able to implement many more projects, allocate much more funds to these initiatives,… nevertheless, the main directions have not been stopped, work continues on them. All our strategic projects have already incorporated elements of the most advanced approaches, for example, due to the implementation of our new Press-Filtration Complex, we expect gas consumption to decrease by 3%,» says Bogdan Svyrydko, Head of the Investment Portfolio Department of Ferrexpo Poltava Mining.
What programs are already being implemented
Ferrexpo continues to implement comprehensive energy saving programs such as:
- «Lighting»,
- «Engine»,
- «Pumping units» and others.
Some programs, such as “Decarbonization of Dump Trucks,” are still only at the stage of development and exploration of opportunities.
LED lighting
Back in 2014, the company completely abandoned mercury lamps and began the transition to safer and more economical LED lighting. Almost all lighting at the main production units was replaced, and street lamps were also partially replaced.
LED lighting is used in some areas, which is regulated depending on the intensity of sunlight in the shop. Total savings amount to more than 1,500 MW per year.
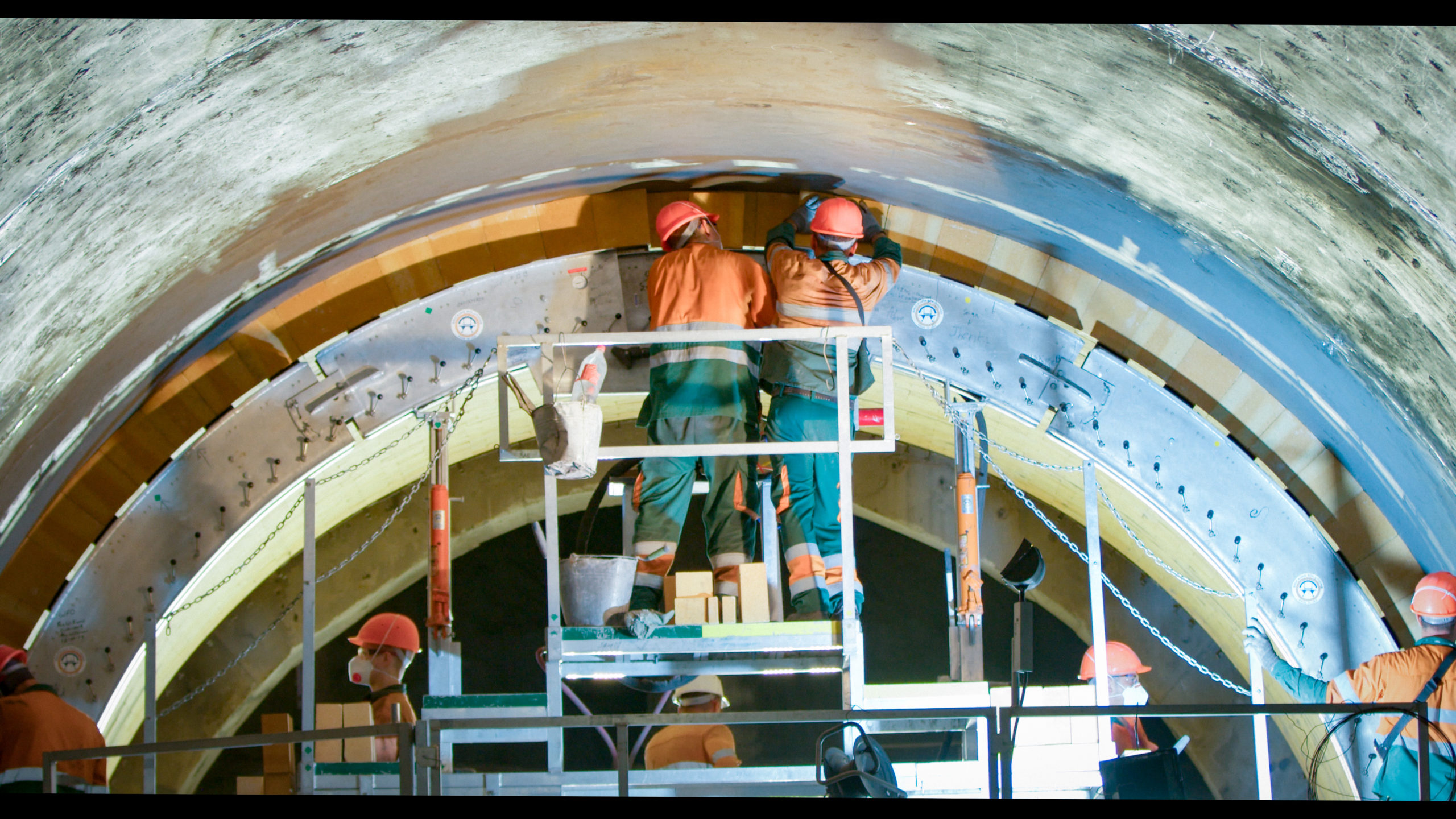
Ferrexpo
Energy efficient engines
The plant completed a program to replace low-voltage electric motors with energy-efficient IE3 class motors. The effect due to increased efficiency and proper utilization of equipment is more than 4,000 MW per year.
During the project implementation, not only low-voltage electric motors were replaced – more than 450 units, but also high-voltage motors – more than 20 units.
Energy efficient pumping units
Starting from 2019, Poltava Mining and Beneficiation Plant has been implementing a program to replace old equipment with more energy efficient one. From 2019 to 2023, more than 100 energy-efficient pumping units were installed. During this time, the energy savings amounted to more than 20,000 MW.
A combined (solar energy instead of using steam) water supply system was launched for the needs of several workshops of Poltava Mining and Beneficiation Plant, as well as a project to heat several divisions of the plant by installing new solid fuel boilers. More than 3 million m3 of natural gas was saved.
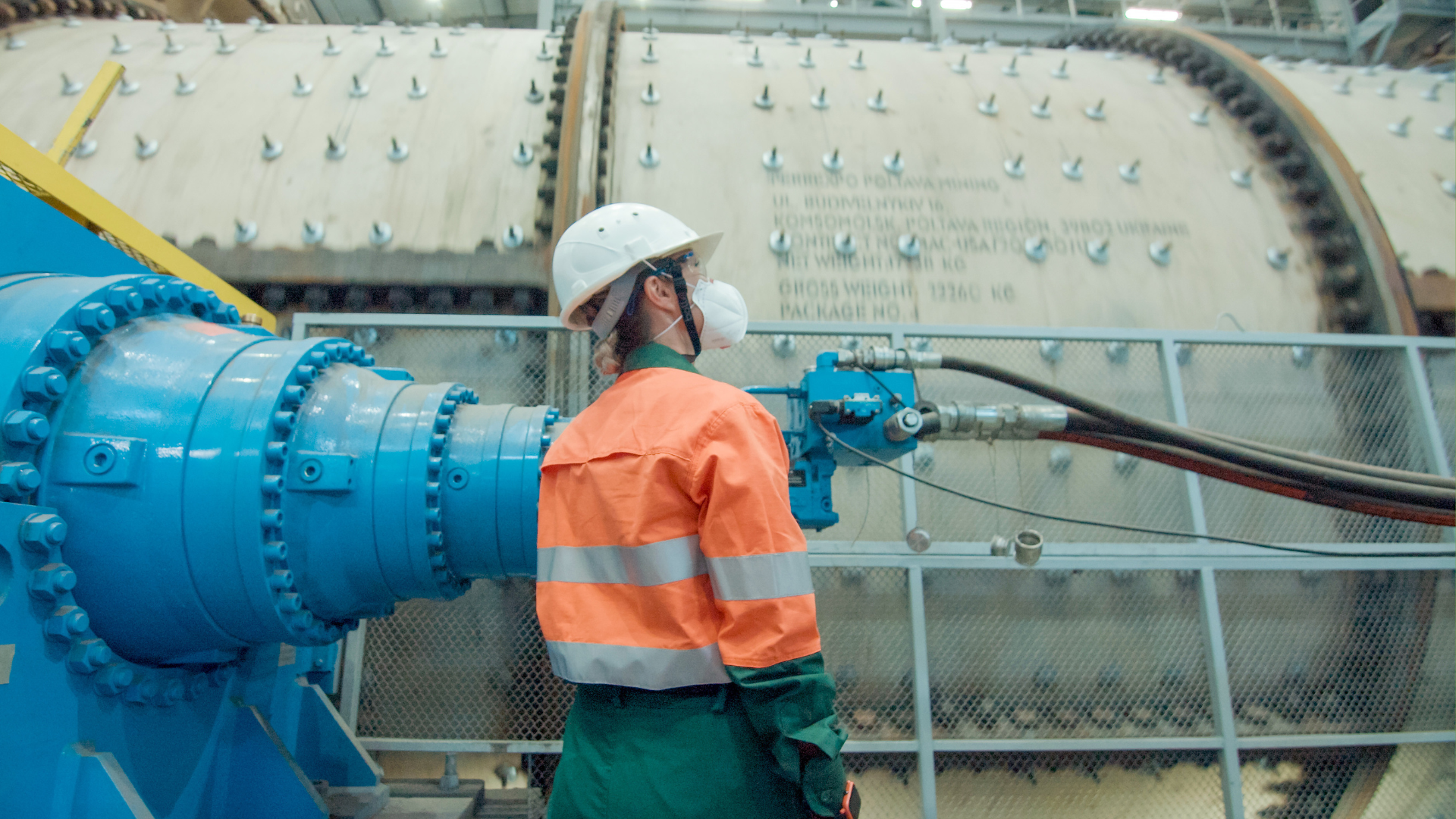
Ferrexpo
Decarbonization of dump trucks
The company intends to reduce emissions from the transportation it uses. For some time now, a team of Ferrexpo employees, in cooperation with equipment producers, has been working on a concept to achieve zero CO2 emissions in mining transportation. The team is exploring several options that could reduce emissions. Each of them requires additional research. Ferrexpo has made significant progress on some of the possible options, but alternatives still need to be explored to select and compare the most effective solution.
“Diesel dump trucks account for up to 30% of carbon dioxide emissions at mining sites. Thus, the decarbonization of the industry as a whole depends on the pace of decarbonization of truck transport. For example, hydrogen-powered trucks are still in the development stage, but their use in the future could completely eliminate CO2 emissions,” explains Petro Protchenko, Operational Efficiency Manager of Ferrexpo Poltava Mining.
There are currently many technological innovations and applied research in the field of decarbonization, some of which are already available for commercial use in quarry trucks. Existing solutions can be categorized into two groups based on CO2 reduction potential on the one hand and Technology Readiness Level (TRL) on the other:
1) Technologies available for immediate deployment: liquefied natural gas (LNG), biodiesel or trolleys. They can already eliminate a portion of CO2 emissions today with modifications to the existing truck fleet and infrastructure changes.
2) New breakthrough technologies: battery electric trucks and hydrogen haulers. So far they are only at the development stage.
The company is still studying the specific parameters and effects of application in the Ferrexpo environment. Which technology is best suited depends to a large extent on local conditions.
Installation of a new press filtration complex
In 2022, the company installed a new press filtration facility that further reduces the moisture content of iron ore concentrate as it leaves the concentrator before pelletizing.
The installed equipment is Metso’s press filtration technology, an example of an upgrade that complements the company’s existing vacuum filtration system.
The benefits associated with the modernization of the filtration facility include:
- Lower energy consumption in pelletizers, where pellets are heated to harden them, due to decreasing natural gas consumption. A 3% reduction in gas consumption is expected. As a consequence, the company expects to optimize production costs and reduce its Scope 1 greenhouse gas emissions.
- Improved product quality, as excess moisture in raw (unburnt) pellets can cause them to crack when heated. The cold compressive strength of the company’s pellets, a key indicator of pellet quality, is forecast to increase by 8% for Ferrexpo Premium pellets (65% Fe).
- Increased material throughput throughout the processing plant, resulting in an average 3% increase in productivity.
- Lower iron losses when processing concentrate into pellets. This will result in an average increase of Fe content in pellets by 0.2%.
To summarize, even during a full-scale war, mining companies continue to invest in the business. Ferrexpo invested $161 mln in the Ukrainian economy in 2022, which corresponds to the average amount of capital expenditures (CAPEX) over the last 8 years – $160 mln. The company maintained the level of investment activity despite the hostilities on the territory of Ukraine. At the same time, Ferrexpo does not stop the process of introducing new technologies at production facilities, which allows it to reduce energy consumption and decarbonize many processes.