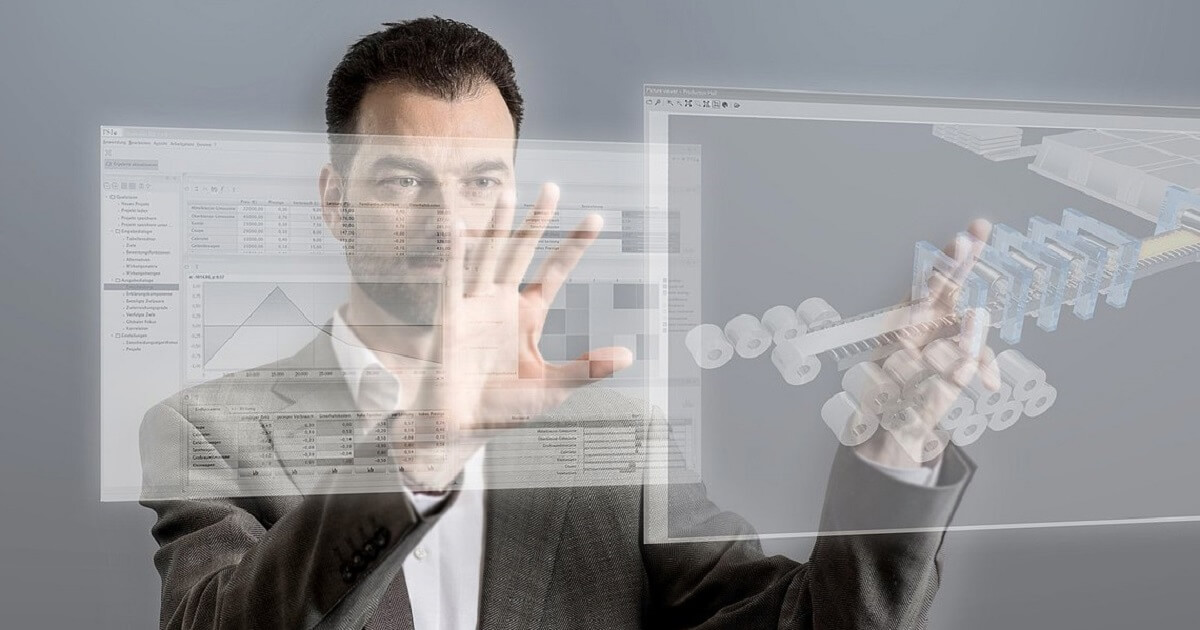
Posts Technologies Ferrexpo 841 10 December 2020
In terms of the level of implementation of Industry 4.0 technologies, industry companies are leaders in Ukraine
Digital transformation creates a competitive advantage: it allows you to increase labor productivity and product quality, reduce costs and reduce losses. In addition, thanks to the introduction of digital technologies, production and sales become more transparent, and the influence of the human factor is reduced.
Research shows that one of the few positive effects of the coronavirus pandemic is to accelerate the digitalization and robotization of businesses. In particular, according to a survey by KPMG in Ukraine, 39% of Ukrainian managers say this (80% of respondents in the world). At the same time, 30% indicated that progress in digitalization has not only accelerated, but has moved the company forward years.
Current level
The size of the budgets for the digitalization of GMK companies is unknown. But in total they can be estimated at tens of millions of dollars, a considerable part of which is hidden within the framework of common investment projects. According to some reports, one of the large GMK companies allocates approximately 0.6% of its gross revenue for its digital projects per year. However, different companies have different needs for digital development.
At least, according to the State Statistics Service for 2010-2018, Ukrainian mining companies invested an average of $4-5 million in software. The peak was in 2013 – $5.9 million. However, it should be taken into account that innovative investments are partly cars and equipment.
The fixed assets of domestic mining and metallurgical enterprises mainly consist of Soviet-era equipment. So, in general, Ukrainian metallurgy can hardly be called a high-tech industry. According to Oleg Shcherbatenko, CEO of the IT-Enterprise group of companies, at industrial enterprises in Ukraine, even the level of basic automation – and this is technology 3.0 – does not exceed 50% on average.
Nevertheless, the professional level of specialists, the level of automation and requests for automation in the GMK is high. The desire to increase its digital level distinguishes the industry from others.
“I would put metallurgists in the first place in the success of the implementation of Industry 4.0 approaches among all sectors of the Ukrainian economy. We see this in the example of AIAE’s cooperation with Interpipe and Metinvest. Moreover, in the structure of Metinvest there is a special division responsible for digitalization – Metinvest Digital. I cannot name other examples of large companies where special staff units in the direction of digitalization would be allocated,” said earlier in interview GMK Center Alexander Yurchak CEO of the Association of Industrial Automation Enterprises (AIAE).
The situation with the introduction of digital technologies at each GMK enterprise is different. According to Oleg Shcherbatenko, some are already moving in this direction, such as Interpipe (IT-Enterprise does all digitalization projects for them). Others are looking towards the introduction of new technologies and are already taking the necessary steps. For example, the company “Metinvest”.
GMK enterprises are characterized by a continuous production cycle. And in such cases, the principle of uninterrupted operation of all components is very important. Increasing data volumes, increasing requirements for response, the scale of production put forward increased requirements in the IT infrastructure and its security.
“For this reason, GMK monitors the regular updating of the server park and data storage systems, expanding the bandwidth and protection of the corporate network, and improving ERP systems (Enterprise Resource Planning – the company’s resource management system). Unfortunately, the instability of the general economic situation leaves its mark on the capabilities of enterprises,” notes Vladislav Maslo, General Director of AM Integrator Group LLC.
Directions for implementation
The main digital transformation tools for metallurgy are the introduction of big data analysis, artificial intelligence and machine learning, the industrial Internet of things, predictive analytics, machine vision, virtual and augmented reality. It is important that all this is to some extent integrated into a single information system.
It would seem, how can you digitalize the equipment produced in the last century? It turns out you can. Data from outdated equipment can be read using modern sensors and transferred to the system for monitoring and analysis.
“At Interpipe Steel, we worked at the level of the MES system (Manufacturing Execution System), integration with equipment and collecting information from sensors. More than 26,000 sensors are installed at the production facility – more than a million different parameters are recorded per hour,” says Oleg Shcherbatenko.
New technologies, such as in steelmaking, can be used to store a history of heat parameters in order to predict the outcome. Or, for example, using machine learning to determine the initial alloy composition and melting parameters in order to achieve a certain quality. This will reduce the consumption of raw materials, optimize the composition of elements, predict product quality, etc.
As Oleg Shcherbatenko notes, the deepest lag in the GMK is in terms of investment in management systems and integrated systems. In this aspect, Ukraine lags behind in almost all sectors, especially when compared with the rest of the world. According to Vladislav Maslo, the following informatization tasks are relevant for GMK enterprises:
- Centralization of disparate data (regulatory and reference information of goods and materials, contractors, pricing, product groups, people, accesses, etc.).
- Ensuring clear communications between departments: both at the level of the current workflow, and at the level of adoption/approval/control of the implementation of management decisions.
- Centralization of information flows – consolidated reporting.
- Business Intelligence (BI) – analysis and forecasting of production and commercial processes.
- Automation of routine processes.
If we talk about individual segments of the GMK, then the modernization of metallurgical production entails the expansion of related IT projects.
“The demand for information storage and processing systems, secure information transmission systems, business process automation solutions has grown. Requests for ensuring the safety of corporate data have become especially relevant – backup storage systems, copying corporate data to the cloud, cyber protection technologies for data,” notes Vladislav Maslo.
Also stable was the need for security systems (especially access control systems and perimeter monitoring) and network technologies. Customers began to show a cautious, but palpably growing interest in hyper-converged infrastructures that combine storage, computing and network resources into a single system, which simplifies the management, protection and scaling processes.
According to Vladislav Maslo, automation of the loading/unloading of ore and other railroad cargo, as well as control over the movement of people and equipment in the mine, remains relevant at mining enterprises. Metallurgists are also actively implementing digital surveillance and monitoring systems.
“For a large metallurgical holding, we implemented an industrial video surveillance system using 450 IP video cameras manufactured by HanwhaTechwin and Axis. Customers needed to track the location of the rolling stock, as well as monitor the situation around and inside the vehicle – a diesel locomotive or a truck. To do this, we have solutions that allow us to record information about an object, to observe its movement,” says Stanislav Yablonsky, head of the press service of the company IT-Integrator.
By and large, a lot of things can and should be automated and digitalized in metallurgy and ore mining – from office operations, sales and logistics, to many production processes. But not everyone.
“There are processes in the MMC that are not yet amenable to informatization. The very process of ore mining is difficult to digitalize, to automate the cleaning of stabs and their premature collapse. There, the entire mining process is initially carried out by a blast wave. Difficulties are also caused by the processes of accounting for extracted raw materials, accounting for losses during enrichment or casting,” says Vladislav Maslo.
Implementation practice
Interpipe Steel production process control system
The main projects of the company “Interpipe” within the framework of digitalization:
- Smart Factory (smart production) – end-to-end order-by-order production planning from order acceptance to shipment of finished products, online traceability of product manufacturing in all stages.
- Smart Logistics is a smart supply chain management, resulting in reduced truck downtime for loading and minimized personnel errors.
- Predictive Maintenance – predictive maintenance of equipment. This allows the transition from the system scheduled preventive maintenance to precautionary service when needed. The necessary data enters the overall system from sensors installed on each piece of equipment through the industrial Internet of things. Big data analysis allows you to make the right forecast and buy spare parts on time.
- Machine Vision – automatic recognition and accounting of the manufacture of products on the production line.
- Machine Learning – recognition and identification of the nomenclature and parameters of documents in electronic document management.
- Smart Devices – a tool for obtaining information for planning and accounting. Using, for example, “smart glasses” frees the worker’s hands and serves as a tool for obtaining information and transmitting a “picture”.
In the near future, Interpipe will focus on the digitalization of logistics and launch an online customer account, where you can see the status and timing of your orders.
(c) metinvestholding.com
Group Metinvest in 2018, its IT division was spun off into a separate company, Metinvest Digital. This company acts as a center of expertise for digital technologies of the entire Metinvest group, and also works with third-party customers. Key digital projects of Metinvest:
- Implementation of SAP Success Factory – a system for managing the performance and goals of personnel, which allows you to set tasks and monitor KPIs and other performance indicators.
- Migration of the SAP system to the cloud platform. Data migration is recognized as the largest in terms of volume in Central and Eastern Europe: 138 systems and more than 18 thousand users work in the cloud.
- Migration of the group’s IT infrastructure (680 servers from two Metinvest data centers) to the Microsoft Azure cloud platform.
- Implementation of a centralized dispatching system for managing railway transportation. The system runs on the SAP platform and is integrated with Ukrzaliznytsya software products.
- The use of drones at mining and processing plants to control the work performed in quarries, assess the volumes of bulk materials in warehouses, create digital models of plants for further planning of construction work, etc.
- Automation of workflow with the use of electronic digital signature (EDS).
- Improving the quality of forecasting gas consumption at metal annealing furnaces in the cold rolling shop of Zaporizhstal based on machine learning.
As of last year, general industrial automation covered about 45% of the production stages and functions of Metinvest. Each enterprise implements various automation and digital transformation projects.
Such efforts of the company were noted this year: Metinvest entered the top 5 best steel companies in the world in terms of digital communications according to WorldSteel.
AT ArcelorMittal Krivoy Rog name such key projects of automation and digitalization in 2019-2020:
Проект | Эффект проекта |
---|---|
Модернизация автоматизированной системы управления технологическим процессом (АСУТП) подготовки шихты аглоцеха № 3 | Замена устаревших весодозаторов на современные производства компании Schenck. Повышение качества дозирования шихтовых материалов для производства агломерата. |
Модернизация АСУТП прокатного цеха № 3 | Миграция АСУТП на базе PLC серии Siematic S5 на PLC Siematic S7. Расширение функционала системы в части интеграции в общую АСУТП систем управления приводами. Расширение информационной емкости АСУТП и ее интеграция с системами верхнего уровня. |
Система WEB-визуализации параметров технологических процессов предприятия | Диджитализация технологических процессов для предоставления оперативной информации об их ходе руководству предприятия. |
Централизация и диджитализация процессов взвешивания грузов | Создание центральной диспетчерской взвешивания грузов с автоматизированными системами распознавания номеров вагонов и формирования отвесных. Разработка единой базы данных взвешивания и ее интеграция с системами SAP, ERP. |
Внедрение системы двухфакторной идентификации в рамках проекта по контролю и учету доступа персонала | В результате внедрения достигнут 100% контроль доступа персонала на территорию «АрселорМиттал Кривой Рог». |
Внедрение систем АСУТП в рамках стратегических проектов: 1. АСУТП машин непрерывного литья заготовок №№ 2, 3. 2. АСУТП коксовых батарей №№ 5, 6. 3. АСУТП агломашин №№ 1, 4 аглоцеха № 2. | В рамках строительства технологических агрегатов внедрены высокоуровневые АСУТП. Обеспечена их интеграция с системами SAP, ERP. АСУТП МНЛЗ 2,3 и агломашин №№ 1, 4 внедрены на базе современных контроллеров Siemens при участии компаний SMS и Siemens Украина. Проект АСУТП коксовых батарей №№ 5, 6 реализован на оборудовании фирмы Schneider и является крупнейшим проектом этой компании в Украине за последние 25 лет. |
Диджитализация процессов технического обслуживания, в том числе поиска неисправностей, систем автоматизации | Применение QR-кода для организации оперативного доступа к технической документации с использованием мобильных устройств с целью уменьшения времени устранения неисправностей в системах автоматизации и сокращения простоев основного технологического оборудования. |
Внедрение информационной системы «Телеграм БОТ» | 1. Общая справочная информация (в т.ч. в режиме вопрос/ответ) 2. Оформление отпусков 3. Оформление спецпитания 4. Получение информации по оплате труда 5. Получение информации по медосмотрам 6. Пенсионное обеспечение 7. Подача заявок в детские оздоровительные лагеря и пансионаты предприятия (использовалась до карантинных ограничений). |
Constantly introduces new technologies and the company Ferrexpo. In July of this year, the Yeristovsky MPP launched a new automatic dispatch center to coordinate the work of the main technological processes (loading and transportation of rock mass, distribution of vehicles, monitoring the performance of machinery and equipment, drilling, etc.). On the basis of the center, it is possible to implement the management of the operation of self-driving dump trucks. The company plans to implement similar projects at Poltava and Belanovsky MPPs.
Even earlier, Integrator Group created an integrated information security system for the financial module in the company, built a server infrastructure for the ERP system and put into operation a module for secure Internet access.
Automatic dispatch center of the Eristovsky MPP. (c) kolo.news
Digital issues
According to a KPMG survey in Ukraine, the main barriers to digitalization are the lack of capital (22%, only 7% in the world) and the lack of a coordinated view of key technology trends (14%).
However, in Ukrainian realities, the key problem is the outdated equipment of steel enterprises. Depreciation of fixed assets in metallurgy is 70%, in the extraction of metal ores – about 60%. At the same time, this figure for the whole country is 61%, in industry – 66%.
Metallurgy and ore mining are very capital-intensive industries. But constant crises and changing world market conditions undermine the investment opportunities of MMC enterprises.
“Even the largest companies of the Ukrainian mining and metallurgical complex do not have so many investment resources, and they try to invest what they have in the re-equipment of production and environmental projects,” Oleg Shcherbatenko notes.
Another problem is the poor understanding and penetration of knowledge on Industry 4.0 among both IT departments and management.
“Many people think that 4.0 is “toys” for IT people. Of course, the IT departments of the company are involved in the creation of the solution, but they are not the customers. The customer of implementation 4.0 can only be the management of the company. Management sees that there are fruits of automation, but it does not understand the effect of implementing level 4.0 solutions. And this affects the allocation of budgets. If I don’t understand what effect it has, then I don’t finance these issues. When management understands what 4.0 gives, then it immediately comes to the conclusion that it needs to be done urgently, yesterday,” explains Oleg Shcherbatenko .
The numbers effect
The digital effect is measured comprehensively – in terms of indicators and characteristics of the level of sales and product quality, customer service, and loss reduction. According to Yuri Ryzhenkov, CEO of Metinvest, the group saves about $50 million per year through digitalization projects. In particular, we are talking about the following innovations:
- Mathematical modeling of the optimal composition of the coal charge for the production of coke. The effect is a reduction in the cost of coal charge by 1.1%. Savings – $ 20 million.
- Using artificial intelligence to control temperature in blast furnaces. The effect is a reduction in the silicon content in cast iron from 0.65% to 0.50%. Savings – $30 million.
Previously Denis Morozov, head of economics and finance at Interpipe, at one of the industry events spoke about the effect of the introduction of 4.0 technologies (as of the end of last year): sales to European countries increased by 62%, in the USA – by 22%. Energy costs for steel production were reduced by 45%, vehicle downtime was reduced by a factor of three.
Despite all the benefits of digitalization, global spending on IT implementation has fallen under optimization. According to Gartner, according to the results of the current year, IT spending in the world is expected to fall by 5.4% to $3.6 trillion. However, already in 2021, we can expect an increase of 4% to $3.8 trillion.
The effect of digitalization is obvious, the process in the country as a whole is going smoothly, but because of this, the prospects and opportunities for digital transformation are enormous.
“These mining companies, unlike large businesses from other industries, have an understanding of the need to strive for the implementation of Industry 4.0, that is, a certain level of maturity. Accordingly, the prospects for digitalization in the mining and metallurgical complex are huge, – sums up Alexander Yurchak. “The more such advanced companies we have, the faster other industries will catch up and develop.”