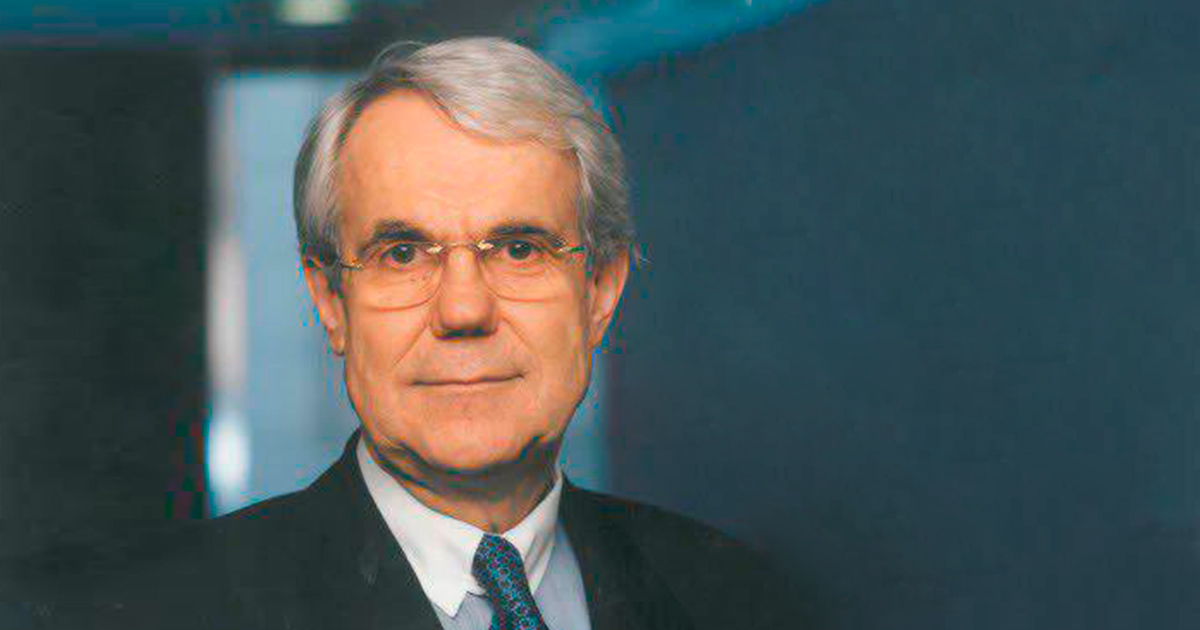
Interviews trends 2272 31 July 2020
Horst Wiesinger Consulting president talked about future of European and Ukrainian steel industry
On July 14th Mr. Horst Wiesinger, the president of Austrian consulting company Horst Wiesinger Consulting, was elected as a Chairman of the Supervisory Board of GMK Center.
We seized the opportunity to ask Mr. Wiesinger how the coronavirus crisis has impacted the European steel industry, whether the EU’s decarbonization plan will be delayed and what he would advise for steelmakers, especially Ukrainian ones, in the current environment.
How badly European steel sector to suffer from coronavirus: your forecast?
— The European and Japanese steel sector are definitely suffering more than the rest of the world. They are serving the high-end of the quality production like automotive industry. This sector experienced a very strong impact of the coronavirus. For instance, the European and Japanese car production is still 25-30% behind the 2019 sales figures.
China has already recovered from the coronavirus crisis and showing an increased steel production in May and June 2020 — 4% compared to 2019. But Europe is still behind by approximately 25% (in the May/June comparison). If not a second wave will occur, I believe that by mid next year the steel capacity will be back on the 2019 values.
Europe has dealt with excess capacity by stimulating steel demand. This turned out to be ineffective since the situation has worsened. Are there any other variants for the EU to reduce excess capacity?
— First of all, we need to decide what the word «overcapacity» means. Obviously, we talk about actual production vs. operable capacity ratio. The capacity decrease in the steel industry is rather expensive due to the intensive capital investment in this sector. So this is one of the main reasons why it is so difficult to decrease any steel capacity.
Could the current crisis force the EU to ease or postpone decarbonization plan for the steel sector?
— No, I do not believe that the EU will postpone the decarbonization. Actually the introduction of new technology and processes would be the most effective alternative for reducing overcapacity.
Will the iron ore demand fall due to decarbonization requirements introduction?
— This will definitely happen.
Who are the most efficient steel producers in the world and Europe now, in your opinion? What allowed them to become leaders: solutions, policies, resources availability?
— I do not like mentioning specific companies. To become an efficient steel producer, you have to focus on cost reduction (by improving asset utilization) and, what is even more important, quality improvement. Available resources would certainly be helpful, however asset utilization and quality improvement with focus on digitalization are the driving forces for the efficiency improvement. Best examples are POSCO and some European producers.
How the digitalization of production processes could increase the efficiency of companies: give the examples? Who are the global and European digitalization leaders?
— Today digitalization is certainly a top trend in the industry. Unfortunately, digitalization is still not widely introduced in the iron and steel industry. However, the most efficient companies are quite digitalized. The PWC study based on the interviews of 157 metals companies’ executives is quite relevant in my point of view. The main conclusions are:
- Metals companies from the survey plan to invest 4% of annual revenue in digital operations solutions over the next 5 years. They are setting themselves ambitious targets for the level of digitization and integration that can be achieved. Nearly two-thirds (62%) expect to reach an advanced level of digitization and integration within the next 5 years.
- Digitization has moved from being a «nice to have» or augmenting capability for metals companies to something that is now vitally important for differentiation and becoming a disruptive force.
- Automation is combining with data analytics to enable much higher flexibility as well as more efficiency in production.
The below figure shows the change of the level of digitalization in the coming years.
In the light of coronavirus crisis and worldwide protectionism, what opportunities for Ukrainian companies do you see?
— For the Ukrainian steel companies the top priority for improving the efficiency will be the quality improvement and digitalization intensifying.
Is the access to iron ore resources the main advantage of Ukrainian steel producers in your point of view? Can the decarbonization and scrap usage intensifying deprive Ukraine of its main advantage?
— The access to iron ore resources utilizing the vertical integration is certainly an advantage. This benefit will not be lost due to decarbonization and increased scrap usage. On a long term (20-30 years), I believe, steel production to be based most likely on a closed recirculation of the scrap (75-80% of the global steel production). To reach this value an appropriate storage of the scrap will be needed (to produce also the highest qualities). This will be, in my opinion, the most severe challenge in the developing of this technology. However, 20-25% of steel production will still need iron ore as a raw material – especially in Europe. Due to this fact there will be still a market for the ore suppliers. The leading ore suppliers – Australia and Brazil – will lose market shares.
What investments would you recommend for Ukrainian steel producers?
— As already mentioned concentration on quality improvement and extended added value chain is the most important recommendation for the Ukrainian steel industry.
Can Ukrainian manufacturers catch up with Russian companies in terms of efficiency? What do they need to do?
— The Russian steel industry invested in the recent years heavily in the improvement of the asset utilization and quality improvement. Again – the Ukrainian steel manufactures have to concentrate on quality improvement especially by improving their actual structure of the equipment and state of the art technologies.