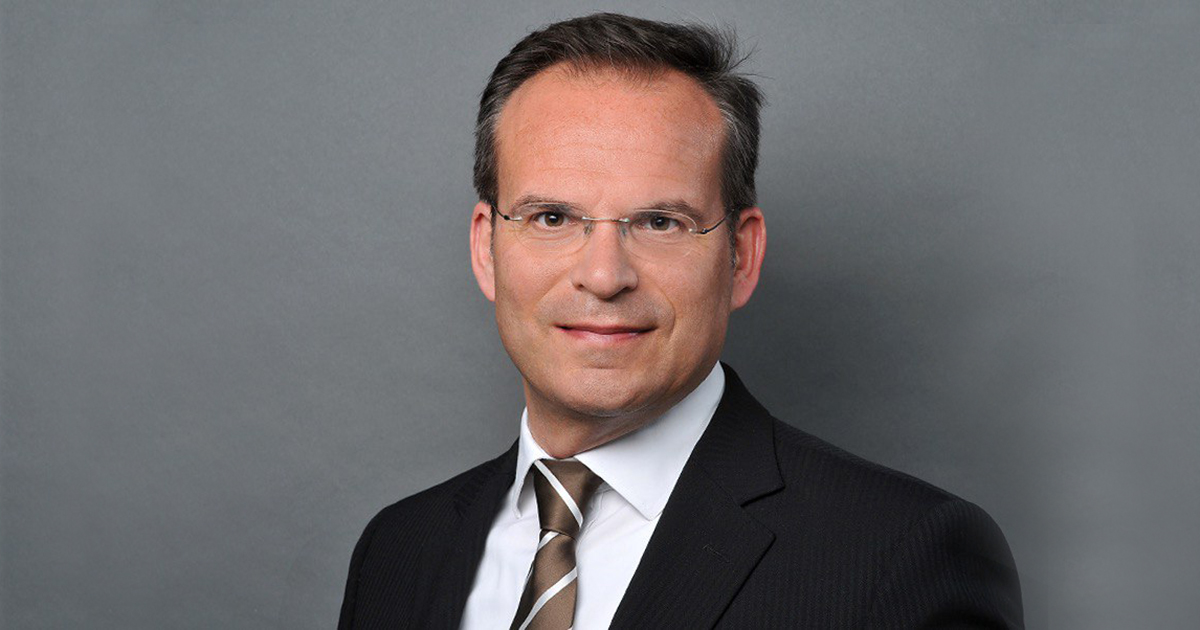
Interviews scrap metal consumption 21541 08 March 2023
The BDSV Public Relations and Public Affairs Officer – about the consumption and supply of scrap for the German steel industry
Germany is the leading crude steel producer in the EU and takes seventh place in the world ranking of producing countries. Less than half of the crude steel output in this country comes from recycled scrap metal. According to the Statistical Report of WV Stahl, the percentage of steel scrap used in crude steel production was between 42.8% and 44.3% from 2016 to 2021. With the plans of the German steel industry to reduce CO2 emissions, the use of steel scrap by local producers should increase. However, the figure will depend on various factors, including energy costs.
The BDSV (German Steel Recycling Association) is the largest steel recycling association in Europe. It represents the interests of companies in Germany that are engaged in the fields of waste disposal services and steel recycling.
Bernd Meyer, who is responsible for public affairs and public relations at BDSV since 2016, told GMK Center about the consumption and supply of scrap for the German steel industry.
What were the dynamics of scrap metal consumption in the German steel sector after 2020?
In 2021, around 45% of the crude steel produced in Germany came from recycled scrap metal. Final figures for 2022 are currently not yet available, but it can be assumed that the steel scrap input ratio has remained relatively constant with minor deviations. The demand for scrap metal is influenced by various factors, including economic activity, availability, and price. The global demand for scrap metal was generally increasing in recent years.
What is Germany’s ranking in terms of scrap metal consumption in the EU? What is the total figure for the EU?
In terms of steel scrap usage, Germany is in the midfield of the EU 27 countries with 45.3 (in 2021). Italy is in first place with an 88% share of steel scrap use. This is because the EAF route has a much higher share in Italy. In Germany, the BOF route dominates with 70%, while the EAF route has a share of 30% of total crude steel production.
In total, the EU 27 consumed 87,9 million tonnes of scrap metal in 2021 (+ 16,7% to 2020). However, it is worth noting that the EU is a net exporter of steel scrap, with exports exceeding imports by a significant margin. Steel mills in the EU do not use as much steel scrap as provided by the steel recycling industry.
What influenced and what was the consumption of scrap metal in the German steel industry in 2022?
Final figures for 2022 are currently not yet available. However, it can be stated that crude steel production collapsed in the second half of 2022.
According to the German Steel producers association, WV Stahl, 36.8 million tons of crude steel were produced in 2022, around 8% less than in the previous year. This marks (with the exception of the Corona year 2020) the lowest annual figure since 2009. The slowdown, centered in the second half of the year 2022, should be seen against the backdrop of a renewed industrial recession, which has its roots in the war in Ukraine, the energy crisis, inflation and continued supply chain problems. Production in the scrap-intensive EAF route fell by 9 % and in the BOF route by 8.2 %.
What is the expected level of scrap metal consumption in the German steel industry in 2023? What will it depend on?
We expect a higher utilization of steel scrap due to the need for CO2 reduction. However, this would depend on the level of crude steel production and energy costs. In general, we anticipate a steady demand for steel scrap in 2023.
How much scrap metal does Germany import? What are the expected levels and geography of supply in 2023?
In 2022, Germany has imported 4.3 million tons of steel scrap. It can be assumed that the amount in 2023 will remain relatively constant. Main suppliers are the Netherlands, Czech Republic and Poland.
What was the export of scrap metal from Germany in 2022? What will happen to exports this year? Who will be among the main exporters?
The total steel scrap exports for German amount to about 7.7 million tons. Germany’s steel scrap exports in 2023 depend, among other things, heavily on how much steel scrap is used in German crude steel production. There will be no shortage of steel scrap for export in the foreseeable future. Within Europe the Netherlands, Belgium and Romania will continue to be the main exporters.
Is there any risk of a scrap shortage in the German steel sector? When and why can this happen?
No, there will be no shortage of scrap steel in the foreseeable future. This will only be the case if the proportion of steel scrap in the steel industry is significantly increased from the current level of around 45%. However, there are currently no signs of a massive increase in the use of steel scrap in steel production, as BOF production still accounts for 70% of crude steel production in Germany.
What measures will help to avoid a shortage of scrap metal?
There will be no shortage of steel scrap in the foreseeable future. Free global markets without trade barriers are essential for the European steel recycling industry.
What will happen to scrap prices in the first half of 2023?
Currently, the supply of steel scrap is scarce, especially obsolete scrap. We expect strong export markets to support steel scrap prices. However, uncertainty in the market is still high. It remains a short term market determined by many variables.
What is the share of electrometallurgy in total steel production in Germany? What will it be in the long term?
In Germany, the EAF has accounted for 30% of crude steel production for many years. As the use of steel scrap in crude steel production in the electric furnace route is almost 100%, this should be further expanded.
What are the decarbonisation plans of the German steel industry? How realistic are they to implement?
EU provides many subsidies, but these are mainly earmarked for hydrogen-based steel production processes.
For example, Salzgitter, a steel producer, intends to gradually substitute coal-based gases required for iron ore smelting with hydrogen. They will allocate 1 billion euros ($1.2 billion) until 2025 to establish a direct reduction plant that will initially operate on natural gas and later on green hydrogen generated from renewable energy sources.
Similarly, Thyssenkrupp plans to adopt hydrogen instead of coal for its blast furnaces. They plan to invest 10 billion euros over a decade to transform their Duisburg site, Europe’s most extensive steelmaking complex, into a climate-neutral facility. Their objectives are to decrease CO2 emissions by 30% by 2030 and attain carbon neutrality by 2050.
Additionally, ArcelorMittal plans to manufacture carbon-neutral steel at its Hamburg site using hydrogen produced from renewable energy sources. They aim to lower CO2 emissions by 30% by 2030 and achieve carbon neutrality by 2050.
These plans are realistic but challenging to implement, as they require significant investments, policy support, technological innovation, and customer demand for green steel products. Germany has launched a funding program for green steel projects worth up to 5 billion euros over five years. From the point of view of the steel recycling industry, the scrap-intensive EAF route should be further expanded due to its positive effect on CO2 reduction and saving of primary resources.