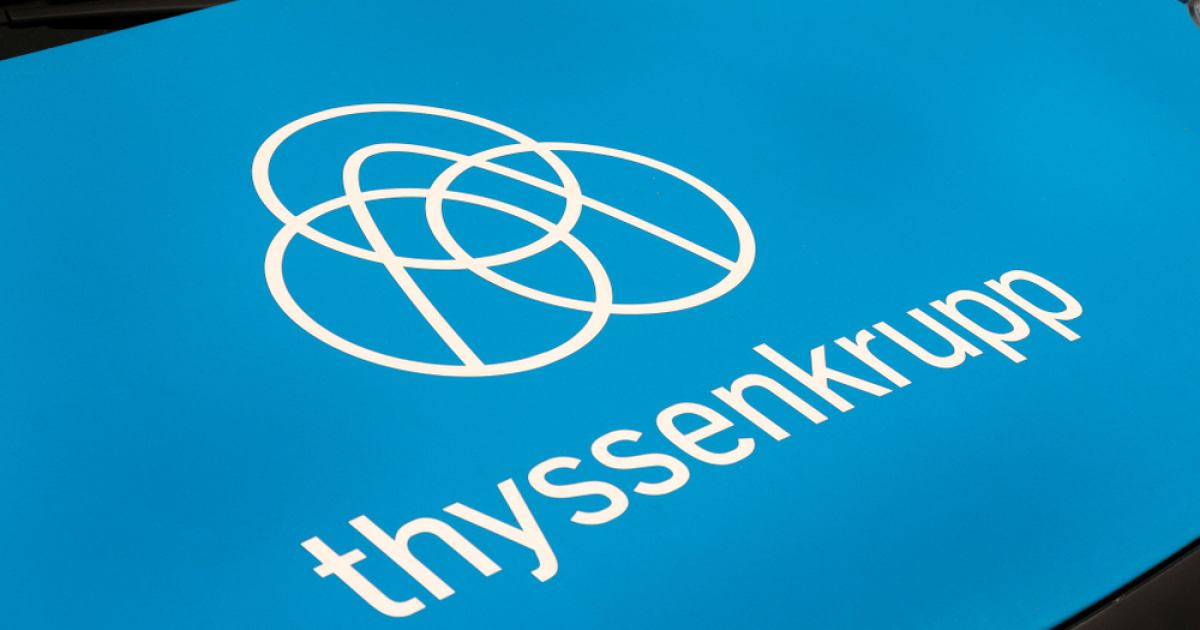
News Companies Thyssenkrupp 1640 13 December 2023
Updated facilities will allow the company to better meet the needs of the market
German steelmaker Thyssenkrupp Steel is launching a major modernization project at its plant in the Bruckhausen district of Duisburg, Germany, MarketScreener reports.
The company recently held a ceremony to mark the start of preliminary installation work at the site where the continuous casting machine No. 4, which will produce slabs, and hot strip mill No. 4 will be located.
The ceremony took place a few days after the opening of a two-stand reversing cold rolling mill at Thyssenkrupp’s Bochum site.
In turn, the project in Bruckhausen involves the division of the existing rolling and casting line into a modernized continuous caster and a hot strip mill. Primetals is the technology supplier, just like in Bochum. The existing integrated mill, the company explained, can no longer meet the high demands of the automotive industry as well as other fast-growing markets. The separation of the foundry and rolling sections will ensure highly efficient production of high-strength steel grades and premium end products.
«Our new and renovated facilities will enable us to meet the changing needs of the market, such as the demand for stronger steel grades, tighter tolerances and optimized surfaces,» commented Heike Denecke-Arnold, Production Director of Thyssenkrupp Steel.
In 2021, Thyssenkrupp Steel placed a large order with Primetals Technologies for a reversing cold rolling mill, a hot strip mill, and two continuous casting machines (slabs). The projects are scheduled for completion in 2025.
As GMK Center reported earlier, in the fall of 2022, ThyssenKrupp Steel completed the construction of a new modern walking hearth furnace at Hot Strip Mill 2 at its Duisburg plant. The furnace has a capacity of about 300 slabs per day. The most important advantage of the new unit is the further improvement of the surface quality of premium plates, which are mainly used in the automotive industry.