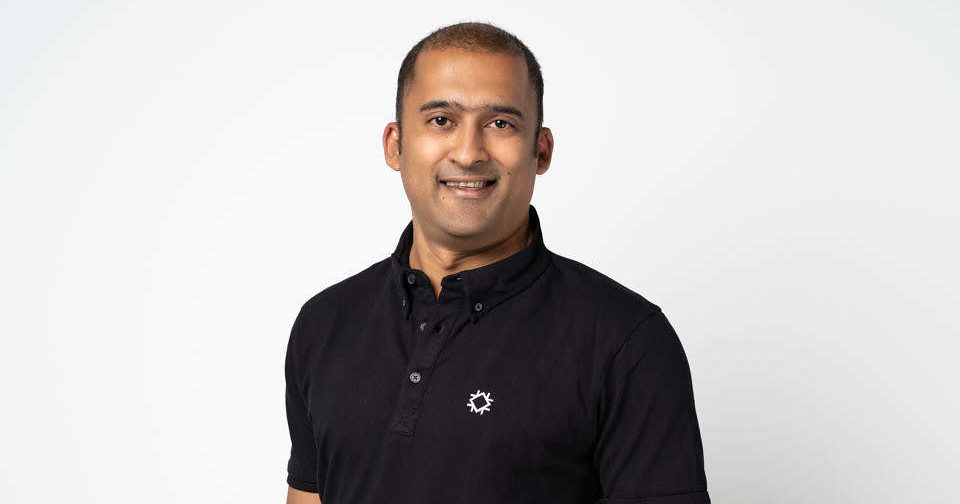
Interviews digitization 12555 08 April 2024
Digitalization allows to optimally finance and support production
Transparency in supply chains is a prerequisite for achieving carbon neutrality, says Neil D’Souza, founder and CEO of Makersite, a company that develops next-generation product data management tools for the global manufacturing industry. He explained why digitalization can ensure the economic and environmental sustainability of industrial companies and what benefits the steel industry can get from implementing modern IT solutions.
What is the role of digitalization and the use of new technologies in the sustainable development of industrial companies?
– In order for industrial companies to balance the fundamentals of economic and environmental sustainability, new technologies are needed to optimally finance and support production while protecting the planet’s natural resources and ecosystems.
Initially, sustainable development was seen as a trade-off between economic growth and environmental protection. As a result, policies aimed at protecting the environment were often implemented at the expense of economic growth and vice versa. Today, however, new technologies and the digitization of databases make it possible to assess the financial and environmental costs of materials and keep this information up to date for a wide range of users across industries-without sacrificing one type of sustainability for the other.
What is your assessment of the recent Antwerp Declaration on the European Industrial Agreement, in particular the requirements of European industrialists to promote the digitalization of innovative research? Why was this topic raised among others?
Technology and the digitalization of industry is the only way we can make meaningful strides to rectify the environmental situation we’ve created as a society. The Antwerp declaration for a European Industrial Deal demonstrates why meeting climate goals requires collaboration and transparency from global business leaders across sectors – this is a challenge no single individual can solve alone, but together we can make meaningful progress toward a more sustainable future.
Which European industrial sectors, in your opinion, are currently moving most actively towards achieving climate neutrality goals? How is the steel industry progressing on this path?
– This is the energy sector, which is the basis for the supply chains of many other industries. This is being driven by the expansion of renewable energy infrastructure through political support, as well as technological investments in energy efficiency and energy storage capacity.
The transportation sector is electrifying its vehicle fleet through stricter emission standards and incentives to reduce the cost of electric vehicles, as well as expanding public transportation infrastructure.
Industry is currently increasing energy efficiency through modernization of equipment and machinery, use of renewable energy sources in operations, use of recycled materials, and circular economy principles, all supported by the ever-expanding ETS and other regulatory frameworks.
The steel industry has great opportunities and is progressing rapidly thanks to the general availability of existing solutions. These include alternative production, such as hydrogen metallurgy and green electric arc furnaces powered by renewable energy; energy efficiency, particularly in heating/cooling or integrated processing to reduce energy losses; increased recycling; and cyclical production.
Why are supply chains the most advantageous area for applying new technologies?
– At the design and sourcing stage, manufacturers determine the costs, environmental impact, and supply chain requirements of their products. Organizations that optimize their supply chains through life cycle analysis (LCA) and product lifecycle intelligence (PLI) see a positive impact on key operational metrics, including costs, risks, and regulatory compliance. By implementing PLI, manufacturers are seeing an average 15-20% increase in profitability, time to market, price premium, and cost of capital.
What benefits can the steel industry gain from implementing modern solutions, such as Makersite software?
– The steel industry depends on a successful supply chain and its maintenance. To remain competitive, manufacturing companies need to fully understand the risks at the deeper levels of the chain.
Achieving transparency across the entire supply chain on an enterprise-wide scale is very difficult. In manual processing, finding and evaluating the necessary information takes several months to several years. It also requires dependence on suppliers to provide information about their supply chains and risks. The Makersite platform offers a modern solution that allows companies to track steel emissions throughout their supply chain, simplifying carbon accounting.
How applicable is the company’s software for tracking supply chains and product life cycles for the steel industry?
– Makersite aggregates data from 140 databases to provide the most comprehensive view of global supply chains on the market. This database details elements across the steel industry, among others, to provide insight into each material and component of a final product. This approach not only supports complex and granular life cycle analysis (LCA) but enables decision-makers to identify the most profitable trade-offs between recycled content, recyclability, and circularity. With Makersite, steel manufacturers and suppliers can make smarter, data-driven decisions that boost sustainability and growth.
Has the company studied the methodology of data collection within the European CBAM? How relevant do you think this data is at this stage? In particular, market participants have previously pointed out the inability to verify the accuracy of the information provided by sellers.
– There is still a lot of confusion about the best approach to collecting data that would be consistent with the EU method for calculating the carbon footprint.
There are two stages. The first is imports, namely how much material is imported that falls into the categories included in the regulation. The second is the quantification of the impact based on the collection of primary data.
In terms of imports, there are two ways to assess this. One can look at data from ERP systems (receipts). Unfortunately, this requires categorizing millions of purchase orders into CN categories and determining the weight of purchased materials, which is often not available in enterprise resource planning systems. This requires a huge amount of effort.
Another approach is to use customs data, however, due to the peculiarities of material imports, different products are often combined into packages, so it is impossible to determine the exact quantity or weight of shipments.
In terms of impact, the European regulation sets a minimum threshold for primary data. This requires cooperation with producers and distributors, who often do not have access to the necessary data. Some sectors are reluctant to share such information for competitive reasons. I don’t think this is due to the inability to verify this data at all, as there are already benchmarks that can be used to guide quality assurance processes. A lot of these difficulties will come to the surface during the first phase of CBAM implementation.
The Makersite platform is the only cloud-based platform that combines data aggregation and live applications for flexible product lifecycle management. Makersite enables companies to manage product viability, cost, and regulatory compliance. The company’s software is used by companies in the construction, automotive, and heavy industries, including BMW, Schaeffler, and Cummins.