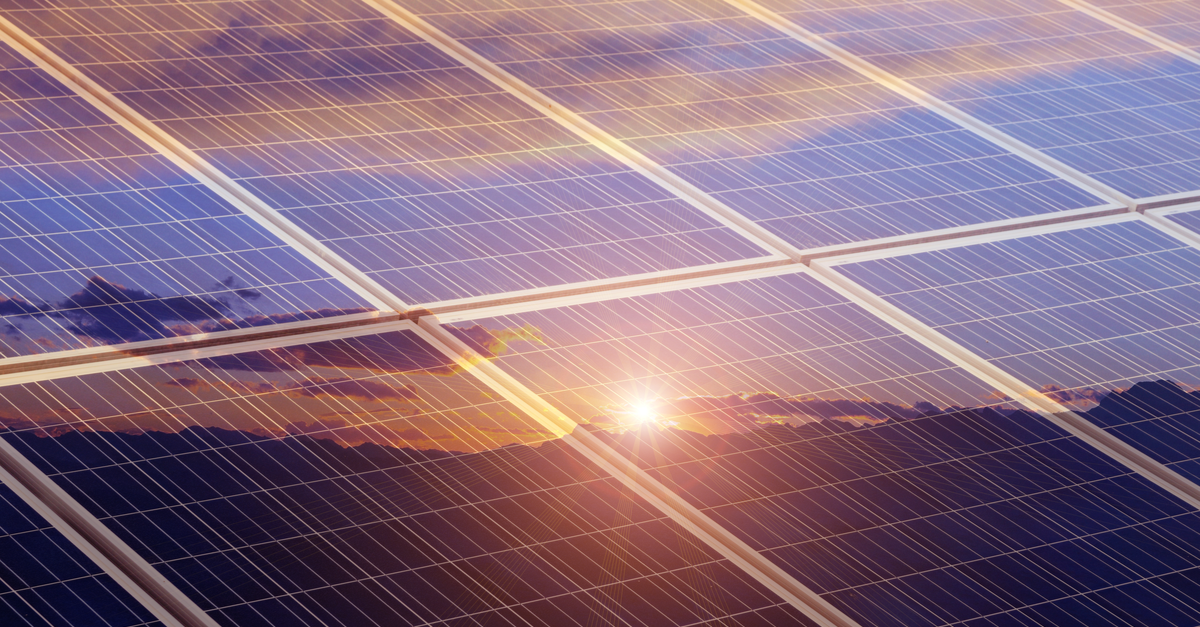
Мнения Индустрия энергетика 778 20 сентября 2021
В погоне за низкой ценой инсталляторы для систем крепления всё чаще используют электросварные трубы
Перегретый «зеленым» тарифом у 2017-2019 гг. рынок строительства объектов возобновляемой энергетики совершил в 2020 году аварийное торможение. Несостоявшийся переход к «зеленым» аукционам фактически означал для участников рынка прекращение массового строительства крупных промышленных объектов. В роли утешительного приза остался частный сектор. На подключение и поставку в сеть электрической энергии, генерируемой домашними СЭС, «зеленый» тариф будет действовать, вероятно, вплоть до 2030 года.
Выстоять 30 лет
Традиционно при монтаже фотоэлектрических модулей (ФЭМ) в землю использовались стальные конструкции, изготовленные из профилей, оцинкованных полным погружением готового изделия в расплав (HDG). А при монтаже ФЭМ на скатную кровлю – алюминиевые анодированные монтажные профили или стальные монтажные периодически перфорированные профили с цинковым покрытием, предварительно нанесенным на рулон (preHDG). Толщина предварительно нанесенного цинкового покрытия на изделиях для внешней среды обычно составляет 16-25 мкм, а при нанесении методом погружения готового изделия – не менее 55 мкм.
При контакте с коррозионными факторами (атмосферными осадками и кислородом) цинк окисляется, образуя барьерный слой оксида на поверхности. Который, в свою очередь, растворяется и смывается выделениями насекомых, пометом птиц. Слой оксида стирается под любым механическим воздействием, после чего окисляться начинает следующий слой покрытия.
За год покрытие может терять 0,5-1 мкм, обеспечивая отсутствие красной коррозии основы в течение 20-40 лет для preHDG покрытий и 50-100 лет для покрытий типа HDG. Поскольку используемые профили имеют небольшую толщину – 1,5-4 мм, а коррозия основы может доходить до 100 мкм/год, то сразу после появления на поверхности ржавчины конструкция теряет несущую способность и за 7-10 лет разрушается.
Принято считать, что жизненный цикл современных ФЭМ составляет не менее 30 лет. Таким образом, лишь покрытие HDG либо алюминий полностью соответствуют этому условию. Алюминий в землю не ставят, в таких системах роль фундаментов обычно выполняют стальные винтовые сваи с тем же покрытием HDG.
Реалии рынка
В сегменте B2C идет ожесточенная конкурентная борьба за клиента-частника. В погоне за низкой ценой качество материалов и оборудования при строительстве бытовых солнечных электростанций непрерывно снижается. Это касается и систем крепления ФЭМ.
На фоне стабильно высоких цен на металлопрокат инсталляторы теперь всё чаще используют электросварные трубы. Единственный доступный метод сборки таких конструкций – электродуговая сварка. Поэтому труба используется черная, без покрытия. После сварки ее покрывают алкидными или нитроэмалями. Чаще всего кисточкой и без соответствующей подготовки: обезжиривания, механической очистки, качественного снятия шлака с тела сварных швов.
В итоге система крепления вступает в коррозионный процесс сразу после окрашивания. Ведь труба, как правило, хранится под открытым небом и уже имеет на поверхности очаги коррозии, которые перед окрашиванием не ликвидируются. Даже если удается качественно окрасить наружные поверхности трубы, внутренняя ее часть останется неокрашенной.
Коррозия внутренней полости труб идет даже быстрее, чем наружной, так как влага там присутствует постоянно. Окрасить стойки, уходящие в бетонные фундаменты, вообще невозможно. А именно точка выхода стойки из бетона подвержена наибольшему коррозионному воздействию. Чаще всего система крепления разрушается именно тогда, когда стоевые трубы критически истончаются в результате коррозии у фундаментов. Даже если собственник будет ежегодно подкрашивать свежую ржавчину, коррозия изнутри трубы ее неизбежно разрушит.
Сварные швы — это очаги более интенсивного коррозионного процесса. При сварке сталей часть материала основы обезуглероживается под воздействием высоких температур. Так как сам шов толще материала основы, то он устоит. Но непосредственно примыкающие к нему поверхности трубы – нет. Через несколько лет вблизи сварных швов появятся раковины, которые в скором времени критически снизят несущую способность трубы.
Навес дяди Вани
Обычно инсталляторы пользуются невежеством потребителя. Чаще всего в ход идет прецедентный фактор. Обычно приводится в пример навес дяди Вани, которого все знают. Навес стоит уже десятый год, и сварен он из трубы. Также нередко установщик предлагает положиться на его солидный опыт – как правило, это 3-5 лет. В ход идут примеры сооружений из длинного сортового проката, которые были возведены в прошлом столетии и стоят по сей день, хотя ни разу не окрашивались. Но главный довод: из трубы дешевле.
Подобная аргументация, конечно, ложная. Труба, которая держит навес, в любом случае находится под ним. А значит – не подвергается коррозионному воздействию атмосферных осадков. Пятилетний опыт ничего не доказывает, ведь жизненный цикл СЭС гораздо дольше. Несущие конструкции из трубы не проходят проектный расчет, а значит, как себя поведет конструкция во время критического снегопада – неизвестно.
Сами по себе электросварные трубы не прочнее эквивалентного по массе С-образного профиля открытого сечения. Поскольку прочность сварного шва таких труб ниже прочности основы, то разрушение элемента конструкции начинается с порыва сварного шва. После этого труба ведет себя как аналогичный С-образный профиль. Преимущество только в том, что отсутствуют открытые кромки металла. Это хорошо для эксплуатации внутри помещения, но губительно во внешней среде в связи с коррозионной уязвимостью. И хотя конструкции советской эпохи успешно служат до сих пор, сравнивать ЛМК (лёгкие металлоконструкции), собранные из длинного комбинатовского проката с толщиной стенки 5-12 мм, с конструкциями из трубы с толщиной стенки 1,2-1,8 мм совершенно недопустимо.
В любом случае полезно осмотреть СЭС возрастом от 5 лет, крепежная конструкция которой изготовлена из трубы. При таком сроке эксплуатации уже явственно видны следы коррозии у основания опор, вблизи сварных швов, а чаще – повсеместно. Также не лишним будет выяснить возможность и стоимость полного демонтажа СЭС с повторным возведением конструкции. Ведь это придется сделать раз или даже дважды за срок эксплуатации станции. Тут-то миф о дешевизне и развенчается.
Ликвидация отраслевого невежества
На первый взгляд, разрушение крепежных конструкций бытовой СЭС до окончания ее жизненного цикла – это личная проблема собственника. Однако не стоит забывать об основной цели такого строительства. Подавляющее большинство частных СЭС строятся ради получения прибыли в виде оплаты выработанной электрической энергии по «зеленому» тарифу. Простыми словами, государство за счет налогоплательщиков полностью погасит затраты на ее возведение в течение 5-8 лет. Таким путем оно предполагает развить децентрализованную микрогенерацию электрической энергии из возобновляемых источников. А развитие подразумевает длительную эксплуатацию с последующим обновлением оборудования уже за счет частного собственника. Какое же это развитие, если большая часть станций разрушатся, едва дотянув до окончания срока окупаемости? Они будут вынужденно выведены из эксплуатации ввиду невозможности восстановления.
Возможность локализации производства фотоэлектрических модулей и инверторов на территории Украины – это спорный вопрос. Хотя такие проекты существуют, они пока не способны вытеснить импортные аналоги. А вот для производства высококачественных оцинкованных металлоконструкций в нашей стране есть все возможности.
Наши металлургические комбинаты успешно наносят цинковое покрытие толщиной до 20 мкм на рулон. Из него можно затем произвести высококачественные монтажные профили, прогоны, балки столов ландшафтного базирования толщиной до 2,0 мм. В Харькове, Запорожье, Киеве, Черкассах существуют современные предприятия по нанесению цинкового покрытия полным погружением в расплав готовых деталей любой толщины. Сами монтажные профили и комплектные оцинкованные системы крепления массово производятся на предприятиях, специализирующихся на эксплуатации профилегибочных станов с перфорацией.
На мой взгляд, эффективное решение этой проблемы лежит в сфере ликвидации отраслевого невежества. В первую очередь это касается инсталляторов, которые лишены возможности производить инженерные расчеты с использованием доступного программного обеспечения. Эту проблему можно решить путем разработки общедоступного альбома типовых решений для систем ландшафтного и кровельного базирования. На уровне потребителя требуется распространение информационных буклетов с общими требованиями ко всем элементам бытовых станций, включая системы крепления. С экономическим обоснованием и реквизитами компаний, которые способны произвести монтаж СЭС на конструкции из металлопроката с соответствующим классом антикоррозионной защиты.