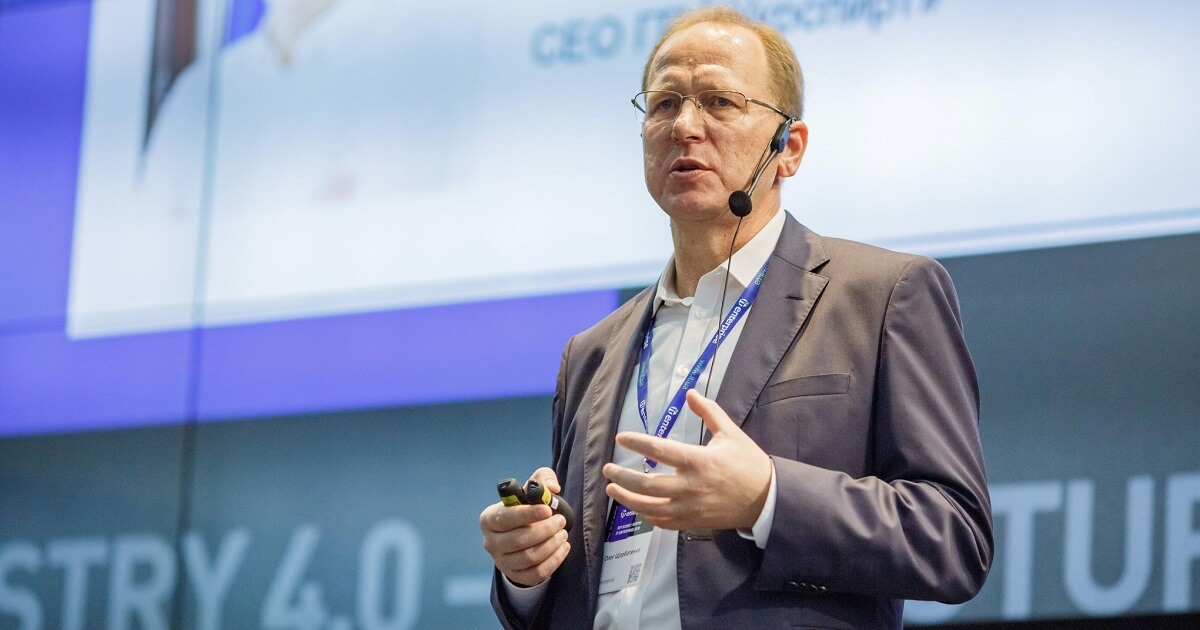
Интервью индустрия 4.0 772 10 декабря 2020
Большинство предприятий в Украине находятся на уровне технологий 3.0 и не всегда понимают суть цифровой трансформации
Всё больше украинских предприятий понимают необходимость цифровой трансформации. В текущих условиях это не прихоть и не дань моде внедрения IT. Цифровая трансформация может стать ключевым фактором повышения конкурентоспособности конкретного предприятия для улучшения его рыночных позиций и оптимизации расходов. А это именно то, к чему стремится весь бизнес.
О проблемах цифровой трансформации в Украине и практике ее внедрения в горно-металлургическом комплексе в интервью GMK Center рассказал Олег Щербатенко, СЕО группы компаний IT-Enterprise, одного из лидеров этого процесса в Украине.
Как вы оцениваете текущий уровень готовности украинских промышленных компаний к цифровой трансформации?
– Мы видим по своим проектам, что большинство компаний не всегда понимают суть термина «цифровая трансформация». Причина в том, что IT-департаменты предприятий часто находятся на начальном этапе осознания необходимости технологий 4.0.
Более того, на промышленных предприятиях Украины даже уровень базовой автоматизации – а это технологии 3.0 – в среднем не превышает 50%. По сути, многим нужна не цифровая трансформация. Они нуждаются в первую очередь в автоматизации и этому уделяют больше внимания. Но автоматизация – это не всегда цифровая трансформация. Главная проблема в этом.
Вы ожидаете, что уровень осознанности топ-менеджмента компаний в будущем повысится?
– Большинство компаний ищут пути развития: ездят по миру, бывают на выставках. Они уже видят успешные и правильные кейсы внедрения новых технологий. Однако компании пока не понимают, как это сделать самостоятельно.
Украинские компании находятся на разных уровнях зрелости движения в сторону Индустрии 4.0. Если говорить о ГМК, то некоторые уже движутся в этом направлении, как, например, компания «Интерпайп». Другие смотрят в сторону внедрения новых технологий и уже делают необходимые шаги. Например, компания «Метинвест».
На предприятиях ГМК немало устаревшего оборудования. Каким образом его можно цифровизировать?
– Данные с устаревшего оборудования можно считывать при помощи современных датчиков и передавать эту информацию в систему для мониторинга и анализа.
Расскажу на конкретном примере проекта. Еще до 2014 года мы работали с Енакиевским метзаводом (ЕМЗ) и Макеевским меткомбинатом. Там мы занимались просто автоматизацией на базе решений 3.0. Оборудование контролировало состояние плавки на ЕМЗ. Датчики получали информацию о параметрах качества каждой плавки, и оно отслеживалось в ERP-системе.
Такое же решение – интеграцию производственного оборудования с датчиками – мы потом создавали в «Интерпайпе».
В чем состояла суть проекта на «Интерпайпе»?
– Мы работаем с «Интерпайпом» с 2001 года. Что толкнуло компанию в направлении цифровизации? Они выпускают продукцию с высокими требованиями к качеству. Но у них была проблема – после 2014 года они перестали работать с российским рынком и российской трубной заготовкой, хотя эти заказы были важны для них.
Строительство нового завода «Интерпайп Сталь» позволило решить многие проблемы как по трубной заготовке, так и по повышению качества продукции. Однако почти полный уход после 2014 года с российского рынка и переход на международные рынки потребовал провести цифровую трансформацию всей системы управления бизнесом. Компания перешла от крупносерийного производства к полностью позаказному клиентоориентированному производству. Теперь «Интерпайп» отслеживает поэтапное пооперационное состояние каждого заказа клиента: от закупки сырья до доставки заказа. Основной KPI – выполнение всех заказов точно в срок независимо от их объема.
В «Интерпайп Стали» мы работали на уровне MES-системы (Manufacturing Execution System – система управления производственными процессами), интеграции с оборудованием и снятия информации с датчиков. На производстве установлено больше 26 тыс. датчиков. В час они снимают более миллиона различных параметров. Эти параметры затем обрабатываются системой. Это уже система уровня 4.0 с элементами, которые являются основой для сквозной цифровизации: интернета вещей, предиктивной аналитики для превентивного обслуживания оборудования, системы Smart Factory, которая работает в режиме онлайн (смарт-каски, «умные» очки, повсеместное использование мобильных устройств). По сути, мы построили цифровой аналог всего производства – Digital Twins, где используются технологии искусственного интеллекта (AI), виртуальной (VR) и дополненной (AR) реальности.
Одна из самых важных для промышленности технологий 4.0 – это предиктивный анализ, который строится на уровне нейронных сетей. Система обрабатывает данные датчиков и на основе технологии машинного обучения изменяет подходы к обслуживанию оборудования. Если раньше на всех предприятиях использовалась методика планово-предупредительных ремонтов или методика оценки состояния, велись дефектовочные ведомости, то сейчас все меняется – вместо человека обслуживание оборудования планирует уже искусственный интеллект. Это дает возможность заранее произвести обслуживание и ремонт, не дожидаясь более серьезных поломок и длительной остановки производства.
Возможно, у других компаний не стояли вызовы такого масштаба. Но без технологий 4.0 «Интерпайп» никогда не достиг бы текущего уровня.
По сути, вы меняли всю систему управления производством?
– Изначально мы стартовали как поставщик ERP-систем (Enterprise Resource Planning – система управления ресурсами компании). Это программный продукт, который охватывает вопросы управления бизнес-процессами. Всё, что там используется – управление производством, закупками, продажами, финансами, себестоимостью, персоналом, бухучетом, – это традиционная автоматизация уровня 3.0.
При переходе на уровень 4.0 меняются сами подходы. В этом случае строится единое решение – комплексная и всеохватывающая система, где от информации с датчика до принятия решений все выполняет искусственный интеллект без участия человека. То, что раньше делалось двумя разными системами – АСУ ТП (автоматизированная система управления технологическими процессами) и ERP-системой, – сейчас в рамках 4.0 уже делает одно решение.
Какие основные проблемы внедрения цифровизации в ГМК вы можете отметить?
– Самая большая проблема – это слабое понимание и проникновение знаний по Индустрии 4.0 и среди IT-департаментов, и среди менеджмента. Многие считают, что 4.0 – это «игрушки» для айтишников. Конечно, IT-департаменты компании участвуют в создании решения, но они не являются заказчиками. Заказчиком внедрения 4.0 может быть только менеджмент компании.
Менеджмент видит, что есть плоды автоматизации, но он не понимает, какой эффект дает внедрение решений уровня 4.0. И это сказывается на выделении бюджетов. Если я не понимаю, какой это дает эффект, то эти вопросы я не финансирую. Когда же менеджмент понимает, что дает 4.0, тогда сразу приходит к выводу, что это нужно делать срочно, еще вчера.
Другими словами, внедрению технологий 4.0 должна предшествовать информационная и разъяснительная работа для менеджмента компаний и их IT-департаментов о преимуществах 4.0. Со своей стороны мы стараемся постоянно проводить такую работу через конференции и другие мероприятия. Например, с этой целью мы провели в 2019 году и в ноябре 2020 года первый в Восточной Европе Форум по Industry 4.0 Trans4mation.
Как вы можете оценить уровень автоматизации и цифровизации украинского ГМК по сравнению с компаниями отрасли в мире?
– Мы сильно отстаем. С одной стороны, в Украине есть много айтишников, которые могли бы работать на внутренний рынок, но украинские компании преимущественно не являются их заказчиками. С другой стороны, даже у крупнейших компаний украинского ГМК не так много инвестиционных ресурсов. А те, что есть, они стараются вкладывать в перевооружение производства и экологические проекты.
Самое глубокое отставание – в части инвестиций в системы управления и комплексные системы. Тут мы отстаем почти во всех отраслях, особенно если сравнить с остальным миром.
Примечательно, что в части количества персонала в IT в ГМК Украины по сравнению с миром наблюдается противоположная тенденция. Украинские компании ГМК имеют достаточно большие IT-департаменты, намного большие, чем где-либо в мире. Это связано со стереотипом о том, что самостоятельно делать что-то дешевле, чем привлекать стороннего подрядчика. Однако этот стереотип уже давно не соответствует действительности. Поэтому наличие громоздких собственных IT-департаментов – это чаще всего пережиток прошлого.
Если все компании ГМК имеют свои IT-департаменты, то в чем необходимость привлечения внешних подрядчиков? Не могут ли компании обойтись своими силами?
– Во всем мире используется такой ключевой подход: предприятие, независимо от отрасли, должно заниматься своей профильной деятельностью, качественно и в срок изготавливать свою продукцию. Если у них есть собственные IT- и R&D-структуры, то их деятельность направлена на потребности производства. В этом случае внедрение новых информационных технологий является очень важной, но непрофильной деятельностью компании. Поэтому в большинстве бизнесов это выносится на аутсорс.
Внешние IT-компании имеют специализированный опыт и персонал, инвестируют большие средства в создание новых технологий, занимаются «тиражными» системами, которые учитывают best practices внедрений многих проектов и т.д. В этом случае менеджмент заказчиков определяет цели, а IT-департаменты заказчиков контролируют работу подрядчиков. Это намного эффективнее.