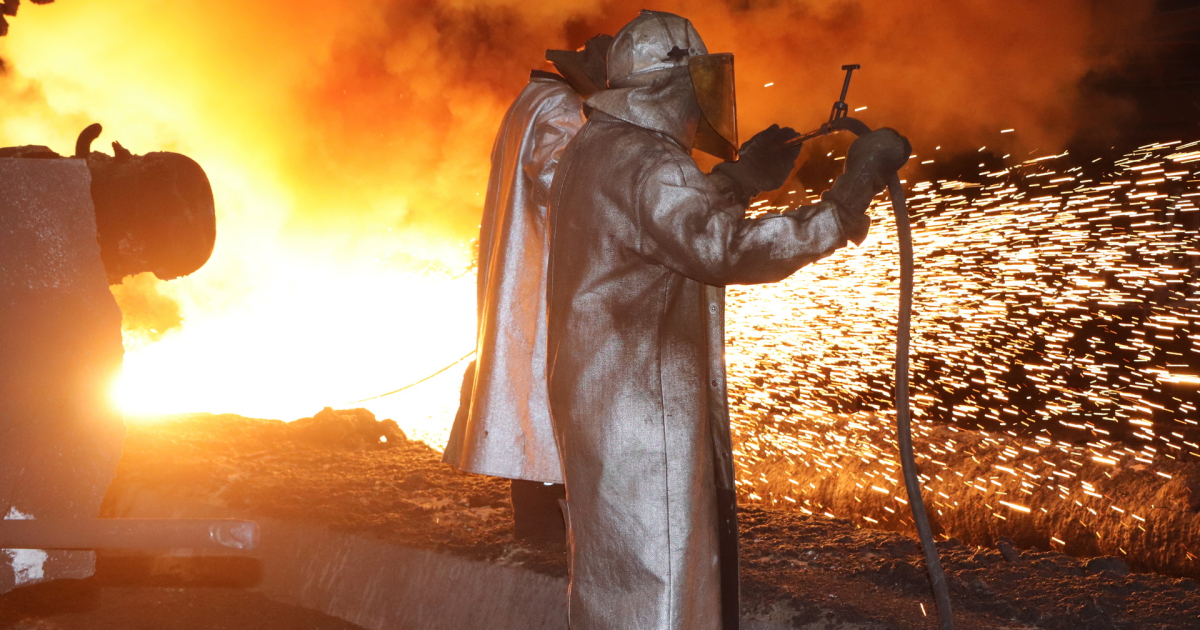
Since the beginning of the year, the actual consumption of conventional fuel has been reduced by more than 15 kg per ton of pig iron
Kametstal Iron and Steel Works implements projects aimed at reducing fuel consumption in pig iron production. This is stated in the enterprise’s press release.
Since the beginning of the year, the plant’s specialists have reduced the actual consumption of conventional fuel by more than 15 kg per ton of pig iron.
«This was preceded by a lot of teamwork, which blasters systematically carry out, including together with the teams of adjacent divisions. In particular, together with the sinter workers, the team goal of reducing fines in the sinter ore was achieved, which made it possible to increase the productivity of the blast furnaces by 2%,» the message says.
In the spring, the blast furnace workshop implemented a constructive solution, according to which swirling devices were installed on all air heaters of blast furnaces. Appropriate equipment improves the quality of gas mixing in the combustion chamber, which, in turn, allows to increase the efficiency of air heaters. The obtained additional temperature of hot blowing also contributed to reducing conventional fuel consumption by 3.5%.
The blast furnace workers also reduced the costs of blowing on the bypass valve СНОРТ, which connects the blast furnaces with the turbo blower, and unplanned idle equipment. This was facilitated by a well-developed system of its preventive maintenance, as well as a decrease in the number of lances that required replacement. In particular, in 6 months of 2023, 40% fewer lances were replaced than in the same period of 2022.
As GMK Center reported earlier, Kametstal improves the quality of sinter ore to stabilize the operation of blast furnaces and increase the quality indicators of the produced pig iron. For 2022, the share of the fraction smaller than 5 mm in the product was reduced from 12.2% to 10.2%, and as of June – to 9%.