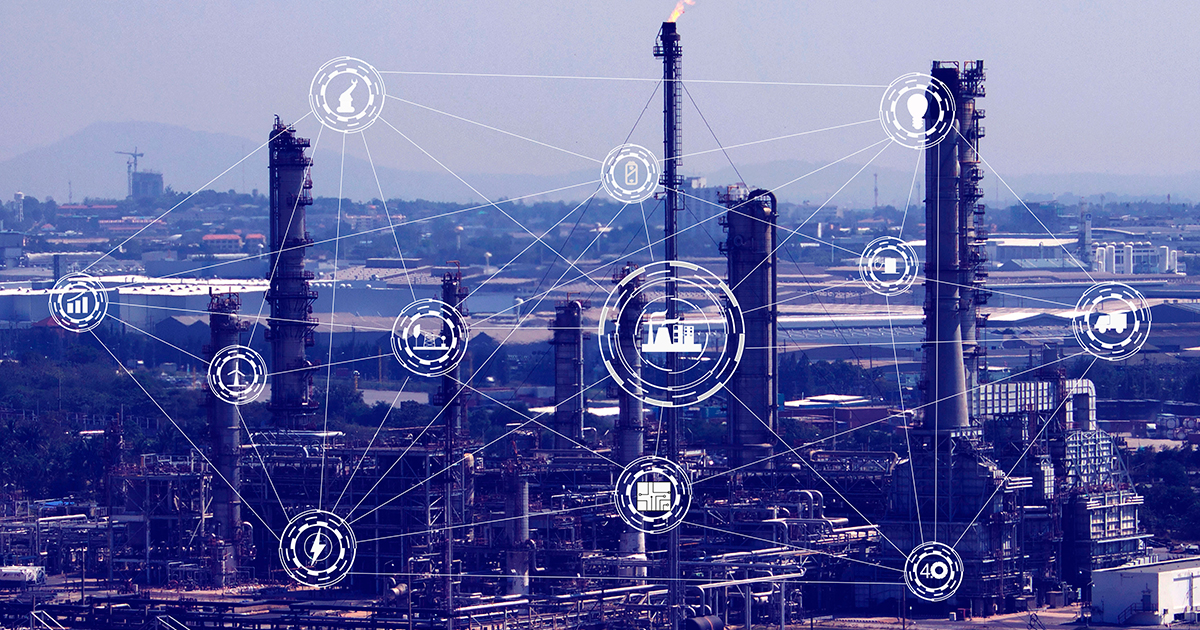
Статьи Технологии 1449 20 марта 2019
Внедрение систем искусственного интеллекта открывает для сталелитейной промышленности новые перспективы роста
Сталелитейная промышленность – один из лидеров «умного» производства. Она активно использует возможности четвертой промышленной революции. Для сталелитейной отрасли «промышленность 4.0» означает практически автономный металлургический завод. Все сотрудники, продукты и производственные мощности на нем взаимосвязаны благодаря интернету вещей (IoT).
Сенсоры на заводе собирают огромные объемы данных. Затем эти данные обрабатывает искусственный интеллект (AI). Это позволяет оптимизировать производство и обеспечить высокую синергию на предприятии.
Мозг процесса
Южнокорейская фирма POSCO владеет двумя крупнейшими металлургическими заводами в мире – в Кванъяне и Пхохане. В 2016 году она произвела 41,6 млн т стали. Ее программная платформа POSFrame собирает большие данные, предоставляемые множеством датчиков, а затем отправляет их AI.
«Раньше у нас было много разных хранилищ данных, но теперь мы перебросили все их сюда», – объясняет Пак Джин Су, руководитель проекта Smart Factory.
POSFrame нужно было многому научиться. Поэтому POSCO попросила своих самых опытных сотрудников помочь в обучении AI.
«Многие из наших ноу-хау хранятся непосредственно в головах наших операторов и инженеров. Наша цель – извлечь эти знания и преобразовать в некий интеллект», – говорит Пак.
Главный принцип POSCO и других производителей стали можно выразить словами знаменитого консультанта и писателя Питера Друкера: «Вы не можете управлять тем, что не в состоянии измерить, и не можете улучшить то, чем не способны управлять».
Безопасность, эффективность и производительность
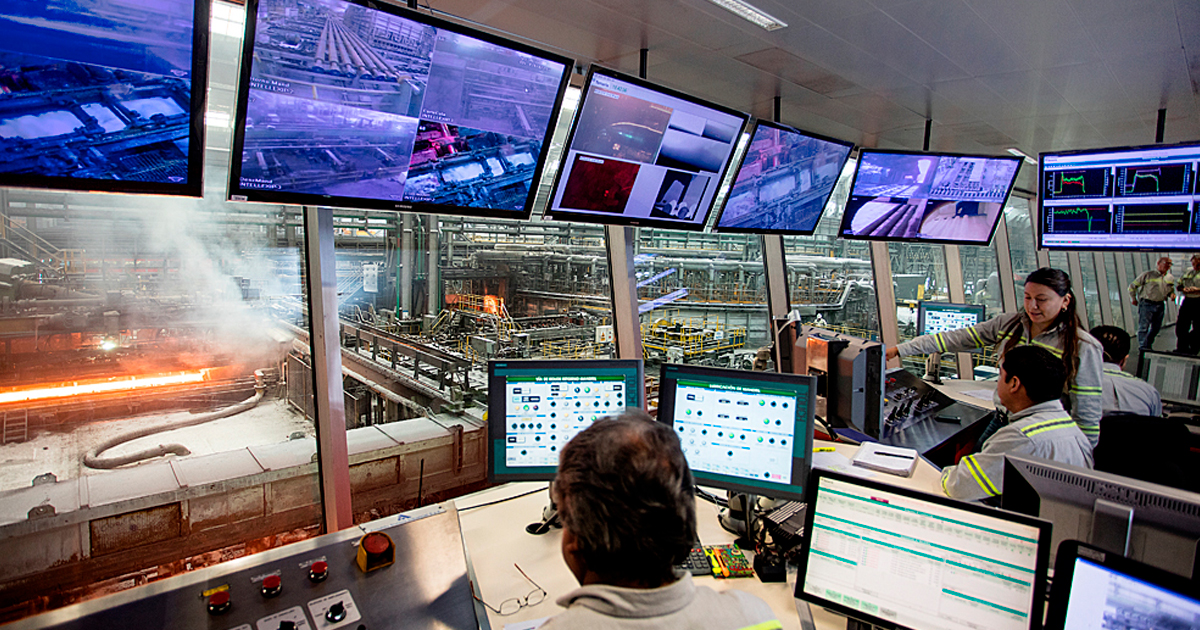
Современные сталелитейные компании, такие как Tenaris Veracruz, Мексика, ежедневно обрабатывают огромные объемы данных
Доктор Франц Андрош, руководитель R&D-отдела австрийского производителя стали Voestalpine, подчеркивает, что именно возможность полного документирования всех этапов производства является основой промышленности 4.0.
«Множество электронных систем измерения и мониторинга автоматически регистрируют, объединяют в единую сеть и используют широкий спектр параметров процесса и продукта. Это облегчает планирование простоев, повышает производительность и гарантирует высокое качество продукта».
Основой традиционного сталелитейного завода является доменная печь. Основа любого «умного» сталелитейного завода – инновации снизу.
Voestalpine уже добилась впечатляющих результатов на своем интегрированном предприятии в Линце. Доменные печи должны постоянно загружаться чередующимися слоями кокса и агломерата. Наличие таких слоев обеспечивает равномерность потока газа. До недавнего времени выявлять температурные нарушения было непросто. Но благодаря технологии 3D-радара Voestalpine смог разработать комплексную модель процесса загрузки, которая позволяет измерять параметры состояния доменной печи в режиме реального времени. Это позволило увеличить общий выход продукта и уменьшить процент отходов.
Совмещение опыта и новых технологий также делает работу на сталелитейных заводах более безопасной. Чтобы получить статус безаварийного предприятия, Nippon Steel и Sumitomo Metal Corporation (NSSMC) пытаются предсказать опасные ситуации до того, как они произойдут.
Инженеры носят «умные» каски, оснащенные камерами, датчиками опасных газов и акселерометрами. Если работник входит в опасную зону, каска тут же подает ему соответствующий сигнал. Если работник упал, каска немедленно отправит предупреждение системе.
Революция данных
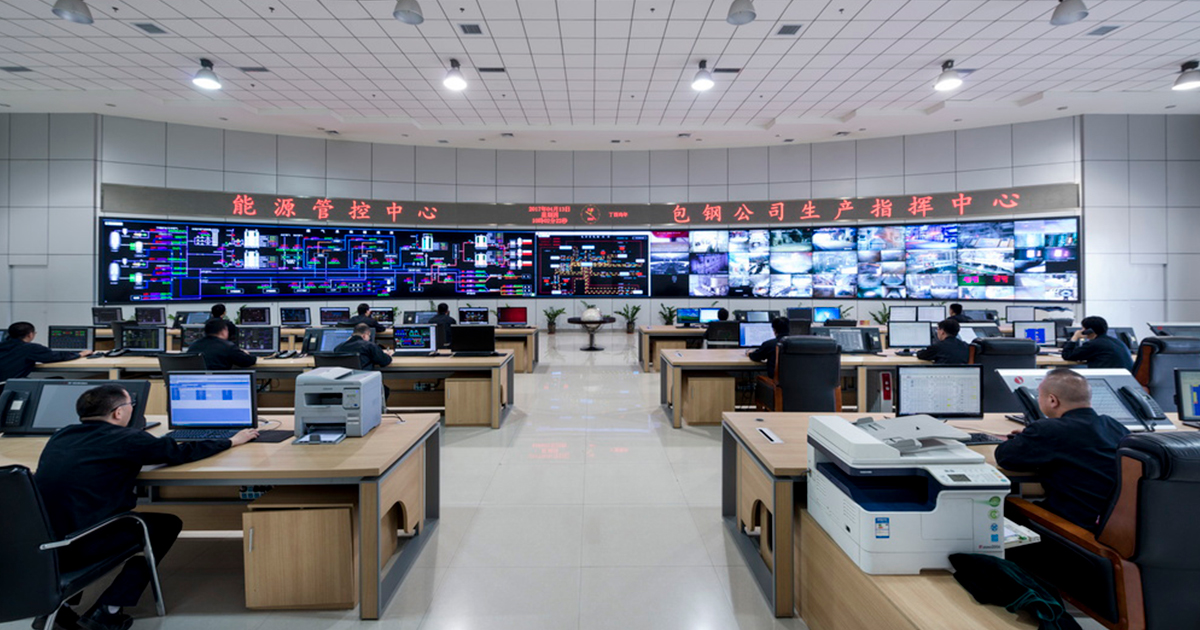
Данные мониторинга в главной диспетчерской в Baotou Steel, Китай
Данные о процессе производства стали были доступны и раньше. Но технологии четвертой промышленной революции открывают новые возможности. Благодаря им производители стали могут собирать больше информации при помощи множества «умных» датчиков и систем, которые обмениваются данными по локальной сети.
Например, когда заготовка попадает в печь повторного нагрева, датчики проверяют воздухозаборник. Результаты передаются AI, который определяет правильную температуру. Затем замеряются температуры верхней и нижней частей заготовки.
«Контролировать разницу этих температур очень важно. Иначе придется направлять заготовку на повторную прокатку, – отмечает Пак. – Заготовку также может зажать в печи. Это может нанести ущерб производственному процессу и стать причиной несчастных случаев».
А еще «умные» заводы открывают новые возможности для обслуживания оборудования.
«Внедряя интеллектуальные данные в наши процессы, мы пытаемся обеспечить более частое профилактическое обслуживание на наших заводах», – говорит Пак. – А это означает не только сокращение затрат, но и уменьшение количества незапланированных простоев».
Сталелитейные заводы работают круглосуточно и без выходных. Невозможно заменить двигатель самолета в полете. Заменять отдельные элементы на заводе почти так же сложно.
По словам Андроша, «цифровая революция также меняет взаимодействие с поставщиками и клиентами: предприятия используют онлайн-платформы, приложения и другие системы, позволяющие отслеживать заказы и другие услуги». Таким образом, она способствует созданию принципиально новых бизнес-моделей.
Экономия энергии
Сталелитейные предприятия используют достижения новой промышленной революции не только для повышения производительности. Они также устанавливают «умные» счетчики и другие датчики, которые позволяют сократить выбросы CO2 и снизить потери энергии.
Многие заводы производят собственное электричество, используя газ из печей и процессы прокатки. Однако другим приходится использовать много энергии от сети, и они всегда стремятся уменьшить расходы на это.
Разные сорта стали требуют разного количества энергии. Современные сенсоры могут точно определить, какие сорта стали наиболее энергоемки. Производители стали могут анализировать цены на энергоносители, чтобы определенные сорта производились при наименьших затратах энергии.
Измерить и улучшить
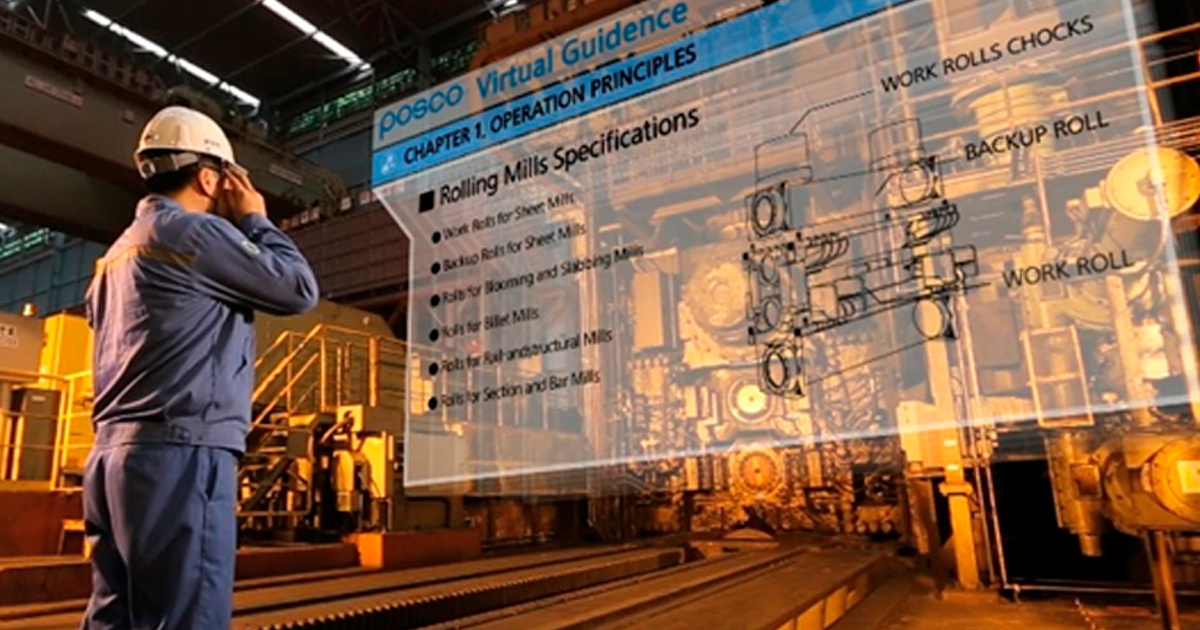
Виртуальное управление скоро может стать реальностью
Искусственный интеллект также позволяет снизить расходы при цинковании. После погружения стали лезвие для резки устанавливается на основе измерений в режиме реального времени. Это позволяет строго контролировать толщину покрытия.
«Если вы переборщите с покрытием в процессе цинкования, потребуются дополнительные затраты», – объясняет Пак.
Используя AI, POSCO улучшила контроль над покрытием с 84% до 99%.
Данные по каждому из процессов становятся частью цифрового кода для каждой заготовки, которая проходит через завод. Количество информации, которую собирает POSCO, выросло в геометрической прогрессии. Это, в свою очередь, обеспечивает качество товара.
«Полные данные позволяют нам точно определить, в какой именно операции и где был допущен просчет, в какую смену, когда и при каких условиях», – говорит Пак.
Такая точность гарантирует полную ответственность и дает производителям стали возможность устранять дефекты путем непрерывных улучшений.
В этом и заключается главная задача внедрения «умного» завода: сбор точных данных. От этого зависят все остальные процессы.
Эффективная команда
Собрать правильную команду – тоже крайне непростая задача. Специалист по данным, который устроился в POSCO, может не обладать необходимыми знаниями в конкретной области.
Чтобы обеспечить успешную командную работу, компания запустила программу, цель которой – привить инженерам POSCO «умную» культуру и способствовать трансформации мышления на уровне группы. Клиенты и поставщики, как и молодые специалисты, также имеют доступ к этой учебной программе.
Несмотря на опасения, что роботы могут лишить людей рабочих мест, внедрение Smart Factory не приводит к сокращению числа сотрудников в POSCO. Происходит перераспределение функций. Меньше сотрудников работают непосредственно на производстве, но больше занимаются анализом данных или разработкой инновационных решений.
«Автоматизированные процессы и техника нуждаются в специалистах, которые понимают, как функционируют роботы, как ими управлять. Это серьезная работа. Поэтому предприятия создают для своих сотрудников специальные курсы и учебные заведения», – объясняет Андрош.
Столкнувшись с растущей конкуренцией – не только со стороны других сталелитейных компаний, но и производителей других материалов – производители стали используют возможности, которые дарит им промышленность 4.0, чтобы повысить свою эффективность и обойти конкурентов.
Перевод Юлии Даниленко
Оригинальную версию текста читайте здесь
GMK Center обладает эксклюзивным правом на перевод и публикацию материалов Worldsteel