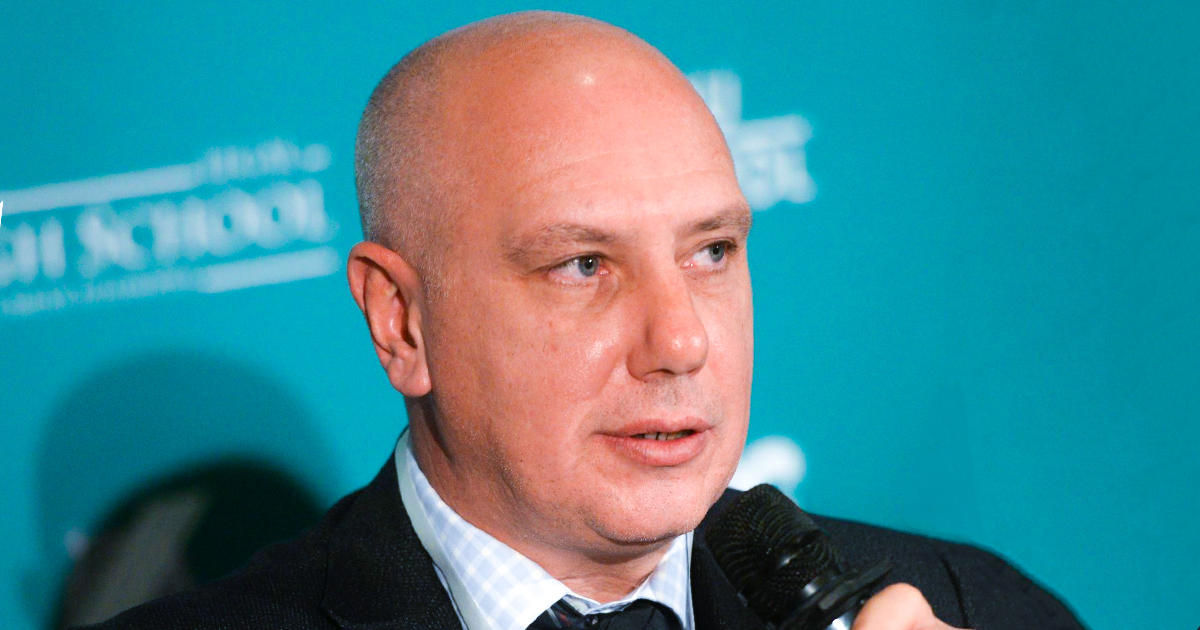
Opinions Industry electricity 1246 12 August 2024
The ferroalloy industry is one of the most affected by the consequences of the war. From the fall of 2023 until the spring of the current year, all production and mining enterprises of the industry were idle. The reasons for this were the presence in the zone of active hostilities and the situation in the energy sector. It is difficult for energy-intensive enterprises of the industry to operate in the conditions of unstable supplies and high electricity prices. However, this has not prevented the production enterprises from launching with minimum load since spring.
Minimum load
Ferroalloy enterprises in 2023 reduced their output by 61% year-on-year – to 210.6 thousand tons. Such a significant drop is due, among other things, to the fact that since November last year the enterprises have gone idle due to active hostilities in the region, high electricity prices and lower prices for ferroalloys on the world market.
Nikopol Ferroalloy Plant (NFP) – the largest ferroalloy plant in Europe – produced 194 thousand tons of ferroalloys last year, while Zaporizhzhia Ferroalloy Plant (ZFP) produced only 20 thousand tons of products. These key enterprises of the industry worked last year at about 15% and 4% of their capacity, respectively.
Also, Pobuzh Ferronickel Plant, which has been idle since November 2022. Its quick restart is impossible due to technical problems and critical dependence on imported raw materials.
The situation was similar for mining enterprises. In 2023, the output of manganese concentrate decreased to 160.3 thousand tons compared to 854 thousand tons in 2022. The only producer was Pokrovsk Mining and Processing Plant (PGOK); another company, Manganetsk MPP, did not produce. Like ferroalloy plants, the Pokrovsk GOK suspended production since November last year due to the rise in electricity prices and other factors.
Since the spring of this year, the production enterprises have been studying the possibility of resuming operations. Such a decision was made, but the actual start-up requires time – to contract electricity, to warm up furnaces. Zaporizhzhia Polar Division resumed operation with two furnaces at 7% capacity since May 1. NFP has been running at a minimum level since the end of June. Now the enterprises are working with the stocks of raw materials, which remained from November last year, and on the amount of electricity they can receive.
Energy component
Ferroalloys production is the most energy-intensive in the entire steel industry due to the use of electric arc furnaces. Before the war, the share of electricity in the cost of production was more than 30%. Therefore, the two most important factors for the operation of the plants are the price of electricity and the stability of supply. Otherwise, an abrupt stoppage of furnaces due to a power outage jeopardizes the safety of the equipment and can have severe consequences.
The only guarantee against blackouts is electricity imports. Since June, the Cabinet of Ministers has guaranteed stable power supply only to those industrial consumers whose imports account for at least 80% of the electricity consumed. The high cost of European electricity increases the cost of Ukrainian products and may worsen their competitiveness on export markets. Ferroalloy plants buy imported electricity, but at current electricity prices the plants will not be able to increase ferroalloy production in any significant way.
Additional negative factors are the increase in domestic prices since June – NEURC price caps for industrial consumers and the attempt of the NEURC to unify the tariff for electricity distribution. This decision was not adopted, but it may still be revisited. In this case, it may lead to a significant increase in the total energy costs of ferroalloy plants.
In July, the Cabinet of Ministers decided not to apply power cuts to the population and facilities in the 20-kilometer frontline zone, which may improve the situation with power supply in the Nikopol region. Earlier, UkrFA appealed to the Cabinet of Ministers and the NEURC with a request to take into account the location of Nikopol in the war zone and to legislate the non-application of capacity limitations and hourly blackout schedules to local enterprises.
Crucial personnel
Due to migration and mobilization, the number of personnel at ferroalloy plants has decreased. The incessant shelling of Nikopol and neighboring settlements became a constant factor, provoking the outflow of people from the region.
The personnel situation at the enterprises of the industry differs from other spheres of the economy. Due to the reduction of production after the beginning of the war and, in particular, downtime since last fall, a part of the personnel was released, although the plants are trying to attract such workers to various types of employment.
On the other hand, if large-scale production plans are set, then there may not be enough personnel, even though specialists in critical specialties are booked within the 50% quota, and training takes years. For its part, UkrFA raises the issue of reserving 100% of personnel for enterprises in the frontline territories.
Expensive logistics
Another important challenge for the ferroalloy industry remains logistics. Although companies in the industry have largely restructured their logistics back during 2022 by moving finished goods warehouses to the western borders, and the sea corridor has partially opened up pre-war export-import opportunities, but costly and capacity constraints remain relevant.
Enterprises have partially transported through Danube ports, but there they have to compete for transshipment capacity with grain and other cargoes, and several stages of cargo handling at once greatly increase the overall cost of logistics.
Risk of losing markets
Production cuts threaten the ferroalloy industry’s export position. In the first half of the year, exports of ferroalloys from Ukraine decreased 11.4 times to 24.2 thousand tons from 275.8 thousand tons in the same period of 2023. Manganese ore exports in January-June amounted to 44.9 thousand tons worth $6.5 million.
Prior to the war, exports accounted for approximately 80% of output, so the risk of losing markets is evident. Our products are becoming less and less competitive due to the increase in production costs as a result of higher electricity prices.
In pre-war 2021 exports were mainly to Turkey (20% of shipments in monetary terms), Italy (14%) and China (11%), while at the end of last year shipments were limited to countries with short logistics shoulder – Poland (53%), Turkey (14%) and the Netherlands (9%). If the trend of production decline continues, partial loss of markets outside Europe and the Black Sea region may become a reality.
Plans and prospects
The most acute problem of the industry is the proximity of assets to the line of contact. The key enterprises of the industry – NFP and Manganets Mining are located just a few kilometers from the front line. Artillery shelling and drone attacks are a daily reality. The ZFP is also in the zone of constant rocket attacks.
In the frontline situation and the general constantly changing situation in the country it is incredibly difficult to plan something, and if plans appear, it is better not to say anything about them. We cannot talk about specific production volumes and plans for obvious reasons. I can only say that the prospects for increasing output depend on acceptable conditions of electricity supply.
Taking into account all factors, the probability of significant increase in production by ferroalloy enterprises remains uncertain. In the near term, military risks will not decrease, and electricity will not become cheaper for the enterprises. In addition, the price situation in the global ferroalloys market is not fully conducive to an increase in production – it has improved compared to last fall, but in general the market is not growing.