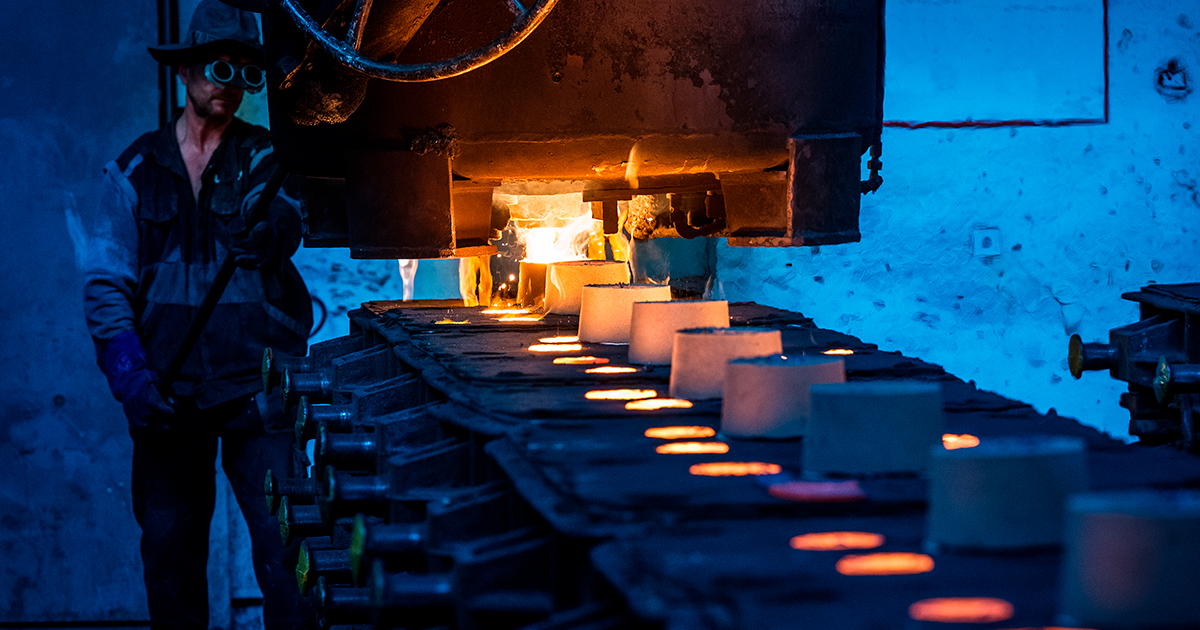
Opinions Industry casting industry 1059 29 July 2019
Ukrainian foundries are expected to achieve the output of 1.5–1.8 million tons per year by 2025
Casting industry is the main supplier of materials for mechanical engineering. The quality of casting products determines the competitiveness of mechanical engineering products in the global market.
Ukraine’s casting industry can manufacture parts of almost any configuration and of any materials. At the best of times, Ukraine produced 6.5 million tons of casting products. The country used to be the world’s top producer in terms of production volumes, 107 kg per capita. Today, it’s only 17–18 kilogram per capita, while developed economies produce 45 kg per capita and more.
Over the past three years, the world’s production of casting products grew from 85 million to 123 million tons. China alone increased its foundry production threefold over the past 5 to 8 years, from 17 million to 47–49 million tons.
By the way, efforts are being made to set up cooperation between Ukraine and China in the casting industry. Since Chinese casting products are mainly of poor quality, China attempts to remedy the situation by placing orders at Ukrainian plants or inviting Ukrainian specialists to deliver staff training. Ukrainian companies benefit from these orders too, because they mean jobs, wages and budget revenue.
Structure of production
The Soviet Union was rather an iron casting than steel casting country: it produced 60% of pig iron casting and 40% of steel casting. Grey iron accounted for the lion’s share in the structure of pig iron production, whereas ductile iron — minor.
The contemporary market, however, demands mostly ductile iron. Therefore, Ukraine is tasked to increase its production volumes.
Production capacity
To date, the capacity of Ukraine’s casting industry is 3–3.5 million tons. Around one fourth of production facilities are located in the separatist-controlled east of the country. Without taking them into account, Ukraine can manufacture 2.5–2.7 million tons. Yet, the existing facilities manufacture only about 700–750 thousand tons. Until 2014, Ukraine produced 1–1.2 million tons of casting products.
In 2015–2016, the sector faced a huge decline — production volumes dropped to 300–400 thousand tons. This was the time of crisis. The sector recovered in 2017–2018. In 2019, production of casting products is expected to reach 700–800 thousand tons.
Until 2025, Ukrainian foundries should reach, according to a conservative estimate, the annual output of 1.5–1.8 million tons.
Domestic market
Ukraine manufactures mechanical engineering products to fill the domestic market. Hence, a growth in mechanical engineering production automatically means a growth in foundry production. These are capacity reserves that will be in demand. Therefore, the lack of the domestic market poses a big problem for Ukrainian foundries.
The second most serious factor of pressure on the casting industry is energy prices. Energy prices in Ukraine are higher than in Russia and Belarus, hence the highest production costs. The country practically cannot compete by price with Russia and, especially, Belarus.
Development of the industry
In view of the above-mentioned challenges, casting companies mapped out a concept of the industry’s development. It covers the following three major directions:
- Application of up-to-date technologies to minimize the influence of the human factor on the result.
- Reduction in casting waste. At present, Ukraine generates 20 kilograms of casting waste per capita, i.e. more than the manufactured casting products per capita. Our task is to cut casting waste by 3–4–5 times, down to 5 kilograms per capita.
- Market protection. We are going to revise our normative and technical documents to protect the domestic market against globalization. We have already revised four basic standards.
The concept implementation will create over 100,000 jobs in Ukraine and ensure annual budget revenue of more than EUR 2 billion.
Key points of the address by Stepan Klymenko at the 5th conference “Ukraine’s Scrap Metal Market: Practical Aspects and Contemporary Challenges” that took place on 5 June 2019