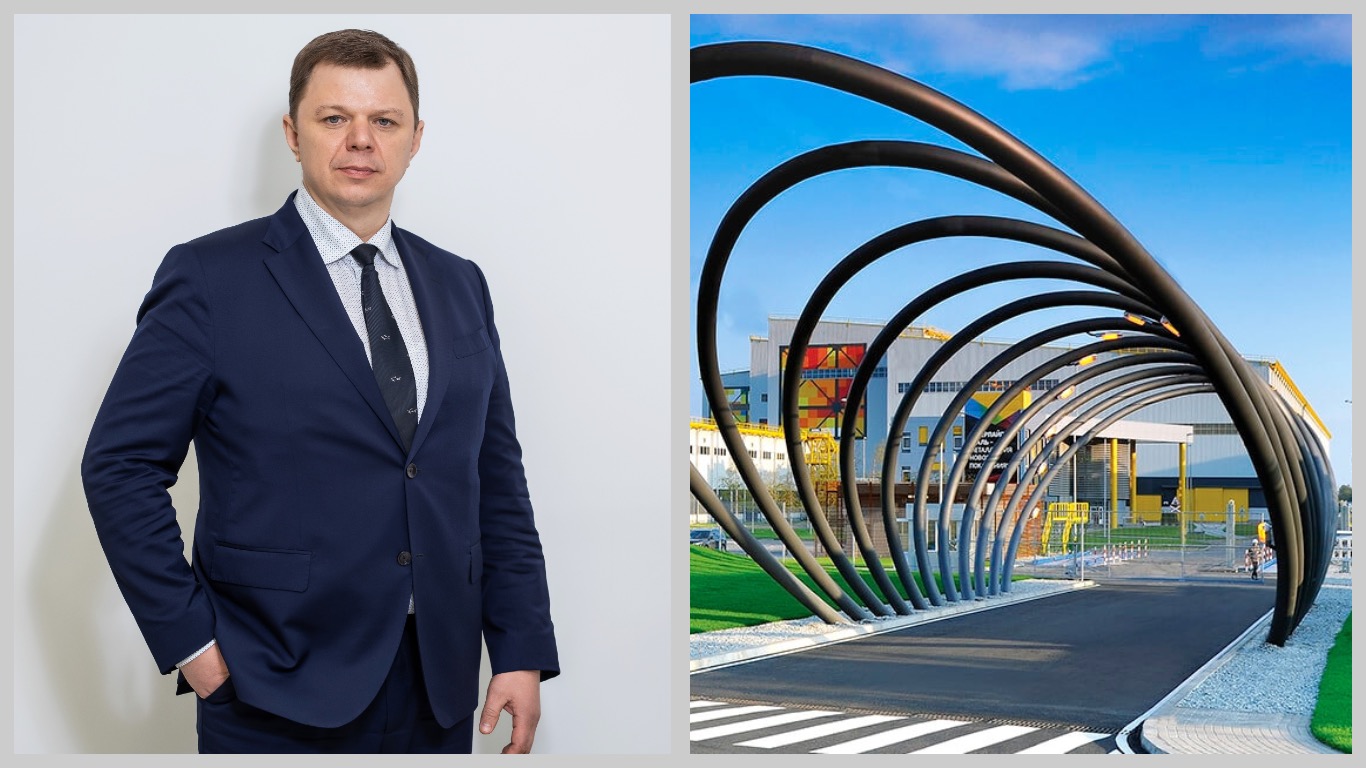
Interviews Interpipe 10278 10 June 2024
Currently, the personnel shortage in the company is 12%, and in some areas – 25%
The full-scale aggression predetermined a wave of problems faced by all Ukrainian iron and steel enterprises – destruction or damage to assets, a drop in production and exports, and logistical difficulties. In the last year, due to staff migration and mobilization of employees, a shortage of labor force has been added, which is no less threatening to production than the problems caused directly by the war.
Due to the specifics of the existing reservation system and recent changes in approaches to mobilization, as the general situation on the labor market, companies in the industry cannot provide themselves with personnel and in the short term will be put on the brink of survival. Vitaly Pakhomov, HR Director of Interpipe, told GMK Center in an interview about the current problems in the field of human resources and ways to solve them.
Mobilization and booking
Let’s start with the topical issues. Will changes in mobilization legislation affect the work of Interpipe companies?
– Yes, with the current approaches to armoring, Interpipe’s plants are at risk of shutting down due to lack of manpower. Already now the staff shortage is 12%, and at some sites even 25%. More than 10% of workers have been mobilized (including more than 20% of men under 60), some people have left irrevocably, the rest is a consequence of the natural turnover of personnel, which existed even before the war.
Since the beginning of the full-scale invasion, for various reasons, we have lost a significant number of personnel, which cannot be compensated by hiring. First, the flow of external applicants, i.e. men of conscription age, has sharply decreased, because women and pensioners can be employed only in some production areas. This has happened partly because of migration to regions farther away from the fighting, and partly because of the fear of immediate mobilization for military registration when hiring.
Secondly, we expect that some people will simply not go on shift because of the increased mobilization laws and the fear of receiving a summons on the way to work or home. According to the law, we can reserve no more than 50% of the active personnel, the rest potentially have to be “given” to the front. The situation is particularly acute in Nikopol, which has been a combat zone since July 2022.
How many employees were mobilized at Interpipe enterprises?
– Over the last year, the number of our employees who serve in the ranks of the Armed Forces or other power structures has been at 950 people. As of today, 61 people have already returned from the army to the workplace on demobilization. Unfortunately, 61 of our employees were killed, 21 are missing, 5 are in captivity. Every second was wounded or treated, every tenth had two or more wounds, needed repeated medical care, some fighters had five to seven contusions, including without hospitalization.
How does the company support its mobilized and demobilized employees?
– Adaptation of demobilized employees has become an important new area of our work with personnel. We now have 61 internal veterans and 15 external veterans. Full medical support is organized for each of them, starting with an in-depth medical examination and ending with rehabilitation measures, as well as outpatient treatment or day care at the corporate polyclinic and repeated medical examinations and treatment when indicated.
In addition, for the adaptation period, a production mentor is assigned to the mobilized person, a psychologist works, and a personal coordinator helps solve organizational issues. All managers have been trained and understand the psycho-emotional peculiarities of working with veterans. For us, this is a continuation of systematic work with the mobilized. Since the first days of the war, the company has had a staff to help mobilized employees. Soldiers are assigned a personal manager whose task is to maintain contact with the soldier during service, during injury and recovery, and after demobilization. We comprehensively accompany our employees at the front: we provide targeted assistance with equipment and ammunition, medical, legal, psychological and organizational support.
In case of death of our employee or his relative of the first degree of kinship during combat operations, the company pays 100 thousand hryvnias as a lump sum, and also permanently supports the families of the victims, where there are children. These are summer recreation programs with elements of psychological rehabilitation, personalized gifts, visits of working teams. In some cases, the company undertakes expensive treatment or lifelong patronage of a seriously ill child of the deceased or his widow.
Businesses in the industry have the right to reserve 50% of their employees. Does Interpipe have such a quota?
– The 50% reservation quota allocated to the steel industry is not enough for us. With the strengthening of mobilization legislation, we may lose most of the other half and we will not be able to replace them. Half of the people on the site will not be able to fulfill the production task by 50%, 20% or 1%. If according to the technology at the rolling mill 10 people should work per shift, but the actual number is 9, it means that people will work with greater intensity and neglect some auxiliary operations, which they will perform overtime. This is compensated materially, but it leads to accumulation of fatigue and cannot last long. But even with this temporary opportunity, we will not be able to work when half of the required number of personnel is on shift.
It is important to keep in mind that the 50% reservation refers to the total number of military personnel in the company, which does not include those already mobilized. In other words, the more of our employees leave under mobilization, the less we can book the remaining ones to work.
In your opinion, what adjustments does the reservation system for steel enterprises need?
– One of the options could be to extend to metallurgy the 100% reservation, which is applied to enterprises in the fuel and energy complex. Another solution could be to actually launch “economic booking” depending on the salary level. That is, when to the current system of 50% reservation is added “economic reservation” for those employees who have non-reserved specialties. If such an option were introduced, I think the company would go to the extent of booking most of its employees.
A good option might be full booking for a certain list of critical occupations that can’t be quickly retrained for. For example, a slinger or stacker can be retrained in a month, while a steelworker, mill driver, turner or CNC machine operator needs to be trained for up to a year to acquire basic skills and qualifications, and takes years to achieve the target qualification.
We believe that the own efforts of enterprises in the frontline regions will not be able to solve the problem of personnel shortage without changing the reservation system. Without such changes, we cannot but rule out the scenario of lower production volumes, which is negative for both the company and the state.
Salary situation
How did the average salary at Interpipe change last year?
– Interpipe is now the industry leader in terms of average salary. This happened after the March salary increase by an average of 20%. If we talk about the dynamics for last year, the average salary of production personnel increased by 37% – to UAH 23 thousand compared to 2022.
Such last year’s growth is explained by the general increase in salaries by 15% in March, the low base of comparison of 2022, which had a lot of downtime, as well as the growth of production volume, which led to an increase in the bonus part of the salary.
In the current environment, not only financial motivation but also other support measures are important. We have fully retained corporate medical insurance, free corporate transportation, and compensation for meals. Quotas for summer recuperation of children have increased many times compared to the pre-war ones, in fact, all requests for summer camp vacations from parents of children aged 7-14 have been satisfied, the company has compensated 80% of the cost of the voucher. It is also important for us to improve working conditions for our employees. We have significantly increased the financing of repairs of living quarters at the enterprises (canteens, showers, etc.).
Tell us how the company built a mechanism for adjusting the remuneration system?
– Our model provides for a general review of salaries in the company for all positions depending on the labor market situation and our production goals. For this purpose, we constantly monitor the salary market in our industry. We also assess the stage of the company’s life cycle. If the company is growing, our salary level should strategically be above the market. We evaluate our business strategy and the success of the company in executing it. And, of course, we take into account our current financial capacity.
At the same time, our revision mechanism is quite flexible, thanks to which we can calibrate salaries within a certain range for a specific specialty, group of professions or for an individual shop, outside the general mechanism of salary revision. This allows us to respond quickly to staff turnover or other circumstances.
Work with personnel
How has the total number of employees at Interpipe group enterprises changed since the beginning of the war to the present day?
– At the beginning of the war, the total record number of our staff was 10,500 and the active number was 10,000. Then there was migration and mobilization, and now the total record number is about 9,500 and the active number is 8,000. The difference arises due to mobilized people who continue to be registered in the state, women on maternity leave and others. It turns out that since the beginning of the full-scale invasion, the number of active personnel has decreased by about 20% or 2 thousand people.
What is the situation with the return of employees who moved to safe regions or abroad at the beginning of full-scale hostilities?
– There have been cases of employees returning, but it is not a mass phenomenon. It is estimated that 30% of those who went abroad in spring 2022 returned. The situation in Nikopol is different. Immediately a few people left the city, up to 2% of the plant’s personnel. The situation worsened in July 2022, when daily shelling of the city began, then 500 more Interpipe Niko Tube employees left in a few days, gradually 200 of them returned.
For its part, the company provides permanent employment and safe working conditions, competitive wages and high social guarantees even under the conditions of military operations. The company reimburses employees 100% of the costs of rebuilding their homes and cars if they are damaged by shelling. Despite the constant shelling of the city, we are now overhauling an administrative and welfare complex for 700 people in Nikopol. This is a good sign for people.
Employees in the combat zone have the opportunity to evacuate underage children together with their escorts to a safe place, the educational process and leisure time are organized there. In addition to their salaries, people receive certificates that they can redeem at food retailers.
What dynamics have been observed in the field of labor protection at work recently?
– The key LTIFR (lost time injury frequency rate) is declining. The war conditions have increased people’s responsibility, including for personal safety.
Personnel shortage
Now the Ukrainian economy is suffering from a shortage of personnel. How acute is the shortage of employees at your enterprises? How can this problem affect the level of production in the future?
– With the current headcount of 8 thousand people, we need 9 thousand for normal work.
First of all, the shortage of people in production leads to an increase in the level of fatigue due to forced overtime. Even despite the high degree of automation and mechanization of production, we have a lot of heavy manual work.
In addition, lack of people leads to negative consequences for equipment. If a person is missing in the production process, it means that some area of the production is left without proper control, and this leads to equipment breakdown or loss of quality. That is why we cannot work for a long time in a situation of understaffing.
Of course, the productivity of older people is somewhat lower, their health is worse, but we are now trying to retain them. The company is also trying to bring retirees back to production.
If this problem worsens, we will be forced to reduce production of less marginal products. This is a standard decision at industrial enterprises in such circumstances.
How does the company solve the problem of shortage of people in production?
– We are working in several directions on this issue.
- Overtime. Our employees realize that there is a need to work for themselves and for those who are now at the front. Therefore, they are loyal to overtime work, which systematically reaches 20-30% of working time per month in some professions or areas.
- Attracting new workers. We have training licenses for all our trades. We hire people from the open market, train them in a certain specialty, skills to work on specific equipment, occupational safety, etc. We hire people from the open market. Approximately 80% of new hires were hired without experience and learned their specialty already on the shop floor.
- Outsourcing. We outsource simple production operations wherever possible.
- Attracting women to production. Men of conscription age are not quite willing to join companies with transparent personnel records, as we have to register them for military service right away. Therefore, we place more emphasis on attracting women to production positions where there are no heavy physical loads. For example, they can be crane operators, quality controllers, defectoscopists, and others. Already now the company has 40% of women on its staff.
- Retention of age staff. We monitor the age structure of our staff. Our goal is to have an average age of 40 years. However, it is difficult to meet such parameters now. In 2021, the average age was 42, and now it is 44. The company is trying to bring retirees back to production.
- Work with young personnel. The Company is trying to attract promising young specialists while they are still in their final years at educational institutions of various accreditation levels. The education system does not currently train specialists of the required profile and level, so we have to retrain them.
The company also constantly conducts advanced training for existing production and office personnel at all levels, covering a wide range of topics -–technology management, safety and hazardous conditions, personnel management, and personal skills development. Last year, about 40% of Interpipe’s employees underwent additional training, who cumulatively mastered 3.5 thousand person-programs.
Interpipe Niko Tube is under daily shelling in Nikopol. How is the safety of people ensured?
– We have installed localized reinforced concrete shelters for those employees who cannot quickly move to a capital bomb shelter in case of danger. These shelters provide reliable protection from shells and drones. The equipment operators’ desks are additionally lined with iron. The employees in Nikopol are constantly trained on safety and handling of explosive objects.
It goes without saying that for working in such difficult conditions, the company pays its employees extra for the increased risk. On average, they earn 20-30% more compared to similar conditions at our other enterprises.