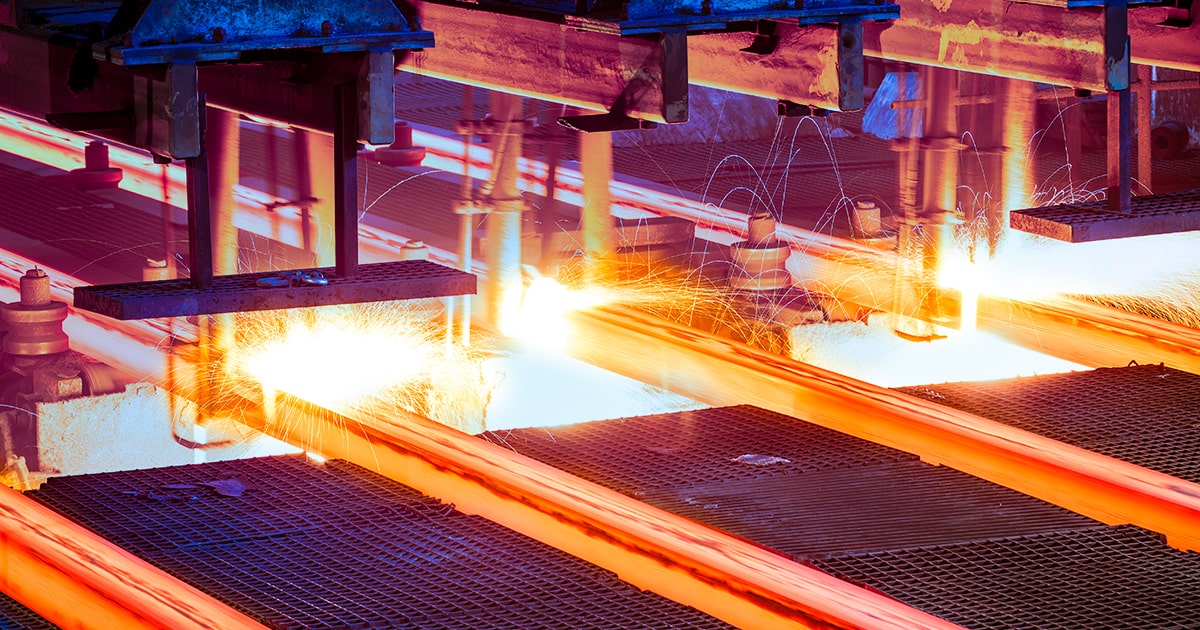
The market is looking for an equilibrium price
In early 2019, prices for raw materials used in steelmaking grew. Turkey, the largest scrap market, was the first to report a hike in prices for scrap, up to 10% on average since the beginning of the year. Companies had to buy scrap at any market price due to the shortage of raw materials, to be able to fulfill their orders.
In the aftermath of the collapse of Vale’s tailing dam in Brazil, the price for 62% Fe iron ore futures jumped within a month from $74.6 to $88.5 per ton. On 8 February, futures quotation reached $92.3 per ton. Vale suspended iron ore mining at 11 plants and alerted some of its customers to force majeure. According to the company, iron ore shipments will decline by 70 million tons per annum.
Steelmaking plants took an advantage of the growing raw materials prices and increased prices for their products. It is possible to say that this is quite reasonable both from the viewpoint of the current market situation and in the context of the previous years’ results, because steel prices have been steadily falling since April 2018 despite a rise in iron ore and coking coal quotations since late summer.
In general, the market is looking for an equilibrium price. According to sectoral sources, some buyers agree to purchase products at the current high prices, fearing that traders’ stockpiles will be exhausted and prices will jump even higher. Others adopted a wait-and-see stance, believing, not without reason, that the current prices are too high.
Apparently, the current rise in prices for semi-finished and rolled products is a regional phenomenon. Turkey and the Middle East were the key drivers of the price growth (+10–15% since the beginning of the year). In the meantime, China did not meet expectations of market participants and increased prices by only 5% on average. The EU market demonstrates different dynamics of prices for steel products, in particular because of the threat of recession in Italy and Germany.
What is most important is that the economy of the main driver of the global steel market, China, is slowing down. Construction activity in China is declining as well. The Central Bank of China is attempting to financially encourage the economy, but it will take time to transfer liquidity from the financial to real sector.
Significant stocks of products at Chinese warehouses are a yet another proof of the weak domestic demand. Market participants fear that in March or April, Chinese manufacturers will have to increase exports to compensate for weak domestic sales. Such scenario may result in an excessive supply of steel products and, consequently, a fall in prices.
Therefore, if the demand for steel products remains weak, prices for both raw materials and finished products will drop. (As a rule, steelmaking plants put pressure on suppliers of raw materials as a response to a declining demand and falling steel prices.) The only exception is iron ore, prices for which are growing due to the shortage. Yet, this factor will remain only until the limited supply of Brazilian iron ore is compensated by supplies from other sources.
P.S. Scrap prices should be mentioned separately. It is important to understand that the growth in scrap demand in Turkey, the main ‘price-setter,’ is a temporary phenomenon. The Turkish steel industry is export-oriented: in 2018, more than a half of Turkish steel products were exported. This year, it will be much more difficult for Turkish manufacturers to export their products due to the globally growing protectionism. Specifically, Turkey has low quotas for exporting rebar and wire rod to the EU and, therefore, will supply less products than the previous year. According to Platts, Turkey has already taken up its semi-annual rebar quota. The Turkish Steel Exporters’ Association expects a 28% cut in exports of Turkish steel products in 2019.