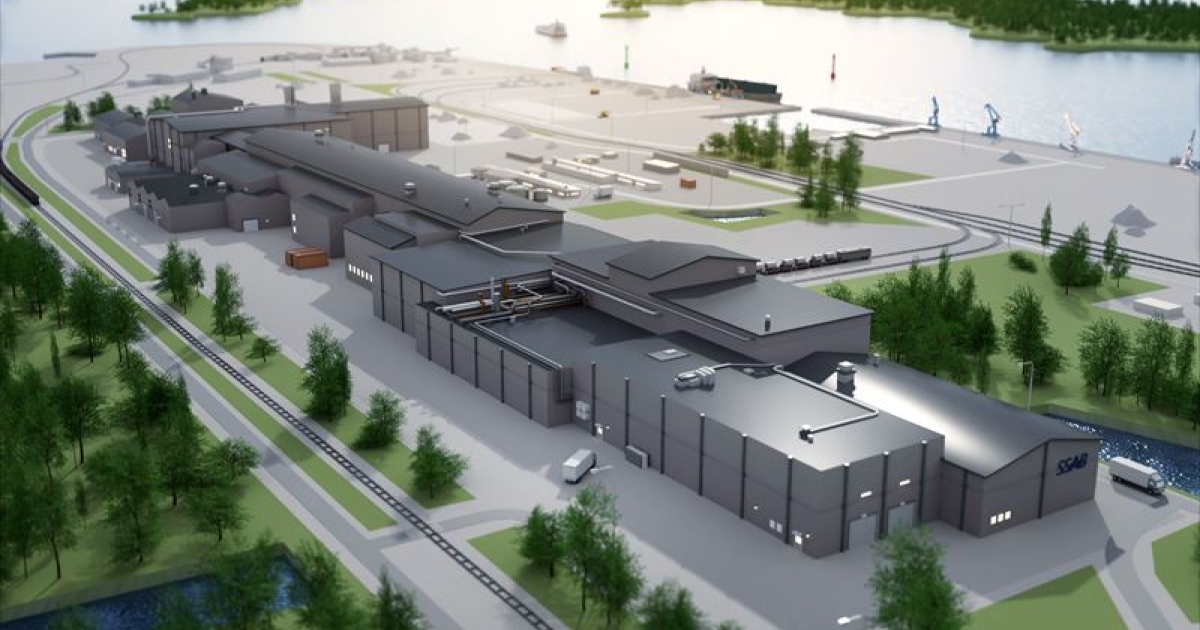
The new plant will reduce CO2 emissions in Sweden by 7% and will be a step towards carbon-free production
Swedish steel company SSAB has received permission from the Land and Environmental Court in Umeå to build and operate a mini-mill in Luleå to replace the existing steel complex. This is stated in the company’s press release.
This project will allow the company to move to carbon-free steel production, significantly reduce its impact on the climate and the environment, and meet the high demand for premium steel.
According to SSAB President Johnny Sjöström, the modernization will be an important step not only for the company but also for the steel industry in Sweden. He emphasized that the new approach will reduce the climate impact at the national level, create jobs in Luleå and strengthen the company’s competitiveness.
The mini-plant will operate on electric arc furnaces using a mixture of recycled scrap and sponge iron produced using HYBRIT technology based on hydrogen reduction of ore.
The change in production technology will reduce annual CO2 emissions by 2.8 million tons, which is 7% of total emissions in Sweden. Overall, SSAB’s transformation will help reduce the country’s emissions by 10%. In addition, the company will get rid of the cost of carbon certificates, increase production efficiency and reduce order fulfillment time.
“This is an important step towards achieving both our own and Sweden’s climate goals, and the faster the transformation takes place, the better it will be for the climate and the environment. We have come a long way to obtain the permit and are very pleased to have received it,” said Sarah Arvidson, SSAB’s Director of Environmental Permitting.
In early December, SSAB announced that it had raised SEK 1.45 billion (€126 million) in financing under the Just Transition Fund, established by the European Union to support the environmental transformation of industry. The purpose of the financing is to accelerate the transition to zero-carbon steel production, including the modernization of the company’s production facilities in Luleå.