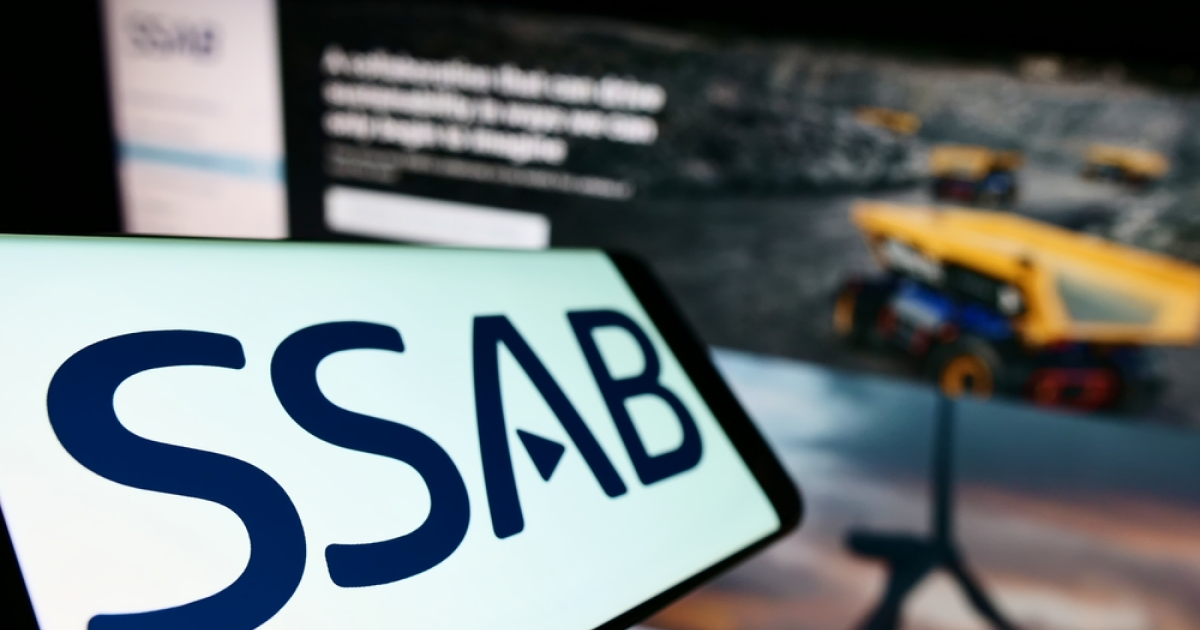
News Companies green steel 1857 23 June 2024
Swedish company to supply SSAB Zero steel to Firth Steels
Swedish steelmaker SSAB and UK-based Firth Steels have signed a long-term agreement to supply SSAB Zero steel, a recycled steel product made using electricity and biogas that does not contain fossil fuels. This is stated in the message of SSAB.
The partnership will help Firth Steels, which is one of the UK’s leading manufacturers of steel profiles for wall and roofing systems, achieve its goal of improving sustainability performance and reducing carbon emissions from its products.
The Swedish company’s steel will be used as a key component of Firth Steels’ brand new Protex Voyage product line, which will provide a low-carbon building solution.
«Scope 3 emissions make up the largest part of our carbon footprint. By forming strategic partnerships with the world’s leading mills, we can significantly reduce these emissions and create a sustainable future for the planet from the start, rather than through offsets,» said James Firth, Managing Director of Firth Steels Limited.
In addition to reducing Scope 3 indirect emissions, Firth Steels has several sustainable initiatives underway as part of a related campaign to reduce emissions from its own operations, including energy consumption (Scope 1 and 2).
As noted, by changing the way it produces steel, SSAB aims to reduce emissions and create a fossil fuel-free value chain with customers and partners, regardless of whether the raw material is scrap or iron ore.
To this end, the Swedish steelmaker has created two unique brands with virtually zero fossil carbon emissions: SSAB Zero and SSAB Fossil-free. SSAB Fossil-free steel is made from iron ore using the unique HYBRIT technology developed by SSAB in cooperation with mining company LKAB and energy company Vattenfall.
As GMK Center reported earlier, SSAB has decided to build a modern, environmentally friendly mini-mill in Luleå, Sweden. The project involves shutting down the current blast furnace-based production system. This will reduce the country’s CO2 emissions by 7%, in addition to the 3% reduction achieved through the conversion of the Oxelosund plant.