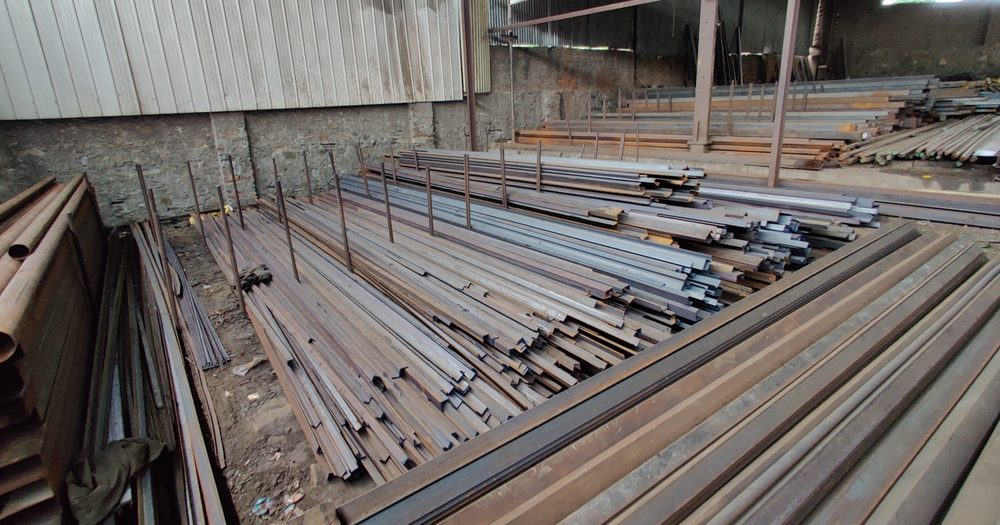
Статті Глобальний ринок залізна руда 303 07 Липня 2025
Уряд країни розпочав трансформацію зі створення нормативно-правової бази
Індійська металургія сьогодні є найбільш перспективною у світі у контексті «зеленого» переходу. За темпами приросту виплавки сталі Індія з великим відривом лідирує серед 10 найбільших країн-виробників. І це попри скромні обсяги експорту та все ще значний імпорт готової сталі. Сильний внутрішній попит п’ятої за обсягом економіки світу вже протягом кількох місяців стримує зниження глобального показника металоспоживання.
Водночас на 1 т сталі в Індії припадає 2,54 т викидів CO₂ за середньосвітового показника 1,91 т. Тобто потенціал для їх зниження колосальний. І в одному дуже важливому аспекті індуси вже випередили інших. Вперше у світі їхня сталь отримала екологічну класифікацію на державному рівні. Тим самим створено нормативну базу для подальшого «зеленого» переходу.
Крок перший: регламентація
Міністерство сталі Індії (MSI) 21 березня 2025 р. оприлюднило Таксономію «зеленої» сталі. Вона набуде чинності у 2026-2027 фінансовому році й встановлює 3 категорії рейтингу. Для присвоєння рейтингу сталь, що виробляється підприємством, має відповідати таким критеріям:
- 5* – при виробництві 1 т готової сталі викиди мають бути менше 1,6 т CO₂;
- 4* – при викидах 1,6–2,0 т CO₂;
- 3* – при викидах 2,0–2,2 т CO₂;
При сумарній оцінці категорій Scope 1 та Scope 2 враховуються у повному обсязі, Scope 3 – частково. До цього розділу включені викиди CO₂ під час виробництва коксу, агломерації й спікання залізної руди, виробництва окатків і транспортування сировинних компонентів.
Присвоєнням рейтингів і видачею відповідних сертифікатів опікуватиметься Національний інститут вторинних сталеливарних технологій (NISST). Критерії рейтингу переглядатимуться раз на 3 роки. Створення та ведення державного реєстру «зеленої» сталі на основі висновків NISST доручено Бюро енергоефективності (BEE).
Влада має намір надавати перевагу такій сталі в межах Політики «зелених» державних закупівель (GPP), яку розробило MSI. Це важливий стимул з огляду на значну роль держави в загальному металоспоживанні.
За даними MSI, у 2022-2023 фінансовому році (ФР) обсяг держзамовлень метпродукції становив 25 млн т. До 2030-2031 ФР він зросте до 67–73 млн т.
Крок другий: оптимізація
Досягти нульових викидів CO₂ в економіці, і, відповідно, у металургії, Індія планує до 2070 р. Це дуже довгий термін, зазначають скептики. Зате реалістичний. За даними Міністерства сталі, вартість питання для галузі – $283 млрд. Це сума, необхідна лише для існуючих метпідприємств із сумарною річною потужністю 200 млн т. Без урахування додаткових витрат на нові заводи потужністю 300 млн т, які планується збудувати до 2047 р.
Але тут йдеться про кінцеву мету – повністю беземісійне виробництво. За фактом же індійська сталь має стати «зеленою» набагато раніше. І коштуватиме це «лише» $13 млрд. У таку суму оцінюється впровадження покращувальних технологій. Насамперед у плані енергоефективності. Зараз питоме енергоспоживання індійських метзаводів на технології BF-BOF становить 6-6,5 ГКал на 1 т сталі, на технології DRI-EAF/IF – 7 ГКал за середньосвітового показника 4,5-5 ГКал.
Шляхи зниження міністерство бачить у цифровізації виробничих процесів. Плюс перехід до використання енергії з відновлюваних джерел (ВДЕ). Зараз індійська сталева індустрія отримує з ВДЕ лише незначну частину споживаної електроенергії.
До 2030–2031 фінансового року цей показник має досягти 43,33 %. Тільки завдяки цьому питомі викиди CO2 знизяться з нинішніх 2,54 т до 2,35 т на 1 т сталі. Як відомо, енергія з ВДЕ суттєво дорожча, ніж вироблена на вугільних електростанціях. Зробити її доступнішою планується завдяки скасуванню оплати за передачу електроенергії.
Серед інших напрямів можна відзначити підвищення ефективності матеріалів для індійської металургії. Зараз вона здебільшого використовує низькоякісну залізну руду.
За підрахунками MSI, збільшення вмісту Fe на 1 % у ЗРС підвищує продуктивність доменної печі на 2 % та знижує споживання коксу на 1 %. Це досягається додатковим збагаченням або агломерацією залізної руди.
Наскільки ці плани реалістичні? ArcelorMittal Nippon Steel India має намір до 2026–2027 фінансового року, тобто в найближчому майбутньому, довести частку відповідності своєї металопродукції «зеленим» критеріям до 70 %. Вже зараз у компанії показник викидів CO2 становить 2,17 т на 1 т сталі. До 2030 р. він має знизитися до 1,8 т. Тобто це цілком реально.
Разом із тим очевидно, що, хоча категорія 5* для індійської «зеленої» сталі передбачає доволі високий рівень викидів (у порівнянні зі США – світовим лідером декарбонізації сталеливарної галузі), вони не є досяжними для комбінатів із BF-BOF. Наприклад, та сама ArcelorMittal Nippon Steel India у 2030 р. не зможе отримати 5* для всієї продукції. Тому потрібні подальші кроки.
Інструменти декарбонізації
На відміну від США, які зробили ставку на R-EAF scrap based, і Євросоюзу, що обрав H2-DRI-EAF, Індія у своїй Дорожній карті «озеленення» сталеливарного сектору не визначає конкретний технологічний шлях декарбонізації. Вона відкрита до використання всіх можливих варіантів. Така гнучкість, безумовно, є перевагою стратегії Нью-Делі.
Сьогодні на електродугові печі припадає 30 % індійських сталеплавильних потужностей. Водночас їх завантаження нижче, ніж у комбінатів із BF-BOF – 74 % і 84 % відповідно. Серед нових підприємств із загальною потужністю 258 млн т на рік на стадіях від проєктування до реалізації частка EAF становить 13 %, або 33,54 млн т. Тут можна відзначити будівництво заводу Tata Steel у Пенджабі продуктивністю 750 тис. т сталі на рік. А також проєкт державної компанії SAIL зі спорудження заводу з EAF потужністю 1,5 млн т сталі до 2029 р.
До 2047 р. Міністерство сталі задекларувало наміри збільшити частку брухту у виробництві сталі з 15 % до 50 %. Для цього знадобляться додаткові поставки, які планують отримати завдяки імпорту. Уже зараз Індія є одним із найбільших світових імпортерів металобрухту – 9,39 млн т за підсумками 2024 р. Очевидно, у майбутньому цей показник може подвоїтися. Наразі імпорт забезпечує приблизно 25 % потреби в цьому ресурсі. Внутрішній збір брухту становить близько 25 млн т.
Разом з тим MSI відзначає складнощі з забезпеченням майбутнього виробництва, коли все більше країн обмежують чи навіть прямо забороняють експорт брухту. Тому Індія реалізує стратегію збільшення внутрішнього збору брухту. У рамках цієї стратегії великі сталеливарні компанії, такі як SAIL і Tata Steel, інвестують значні кошти у власну заготівлю брухту.
Також влада має плани зі створення загальнонаціональної електронної платформи для торгівлі металобрухтом. Це має сприяти «детінізації» індійської заготовчої галузі. Крім того, вже діє програма, яка пропонує власникам вживаних авто стимули для утилізації. Розглядається і можливість обмеження експорту сталевого брухту, обсяги якого, втім, невеликі: 8175 контейнерів у 2023–2024 фінансовому році.
Ще одним напрямком є технологія CCUS, яка передбачає уловлювання, утилізацію та зберігання CO2. В індійській металургії є декілька пілотних проєктів зі збору CO2. Проте наразі вони нерентабельні: поточну вартість уловлювання MSI оцінює у $45–60/т. Для металургійних заводів прийнятною є ціна менш як $20/т, а утилізація та зберігання додають ще $300–500/т. У такому випадку готова сталь подорожчає на 100 %. Тому ведуться пошуки технологічних рішень, здатних зробити CCUS більш доступною.
Як відомо, Індія – світовий лідер з виробництва DRI. Але лише 5 % обпалювальних печей працюють на природному газі, решта – на вугіллі. Тому ще одним напрямком скорочення викидів є газифікація цього виробництва. Цим шляхом пішла компанія Jindal Steel: вона побудувала установку газифікації вугілля на заводі у штаті Одіша. Отриманий синтетичний газ використовується для відновлення заліза у котках до 99,99 %.
Загалом уряд ставить завдання досягти річного обсягу газифікації вугілля у 100 млн т до 2030 р. З цією метою державна компанія Coal India Ltd. (CIL) створила спільні підприємства з Bharat Heavy Electricals Ltd. та Gas Authority of India Ltd. (GAIL). На відповідні проєкти виділяється державне фінансування у розмірі 3,61 млрд.
І ще залишається водень – а саме заміна коксу та вугілля на Н2 у печах для виплавки чавуну й виробництва DRI. Поки що цей напрям перебуває на пілотній стадії. Tata Steel у квітні 2023 р. провела успішне пробне впорскування водню у доменну піч на комбінаті в Джамшедпурі. А у лютому 2025 р., тобто через два роки, компанія повідомила про розробку труб зі спеціальної сталі, яка дозволяє транспортувати газоподібний Н2 під високим тиском.
Можна помітити, що роботи просуваються не надто швидко. Однак насправді для Tata Steel та інших сталеливарних компаній немає сенсу форсувати технічні зміни, оскільки сама воднева індустрія розвивається повільно.
Національна місія з виробництва «зеленого» водню (NGHM), прийнята у січні 2023 р., передбачає випуск 5 млн т продукту до 2030 р. Проте лише наприкінці червня цього року корпорація Adani Group змогла запустити першу в країні установку з потужністю електролізера 5 МВт у штаті Гуджарат. У поточному році група JSW також планує ввести в комерційну експлуатацію завод із виробництва H₂ з потужністю електролізу 25 МВт у штаті Карнатака.
Таким чином, ціль NGHM до 2030 р. точно не буде досягнута. Причина – занадто висока собівартість H₂. Наразі вона складає $4,6-6,3/кг, за даними Institute for Energy Economics & Financial Analysis. У цьому році уряд скасував плату за передачу електроенергії, знизив тариф на розподіл е/е та ПДВ для виробників «зеленого» водню. За рахунок цих заходів, за оцінками IEEFA, собівартість зменшиться до $3–3,75/кг.
Але цього недостатньо. За даними Міністерства сталі, ціна в межах $1/кг зробить використання H₂ комерційно обґрунтованим для індійських металургійних заводів. У такому разі вони зможуть споживати близько 1,1 млн т на рік. Тому, очевидно, уряду доведеться шукати додаткові механізми зниження вартості виробництва «зеленого» водню.
Загалом розрахунки MS свідчать про реалістичність декарбонізації індійської металургії. За наявності «зеленої» премії у 30 % до ціни звичайної продукції, із заміною 20 % виробництва BF-BOF на безвикидне – «зелена» сталь збільшить вартість інфраструктурних проєктів лише на 1,1 %, виробництва авто та побутової техніки – на 0,5–1 %. У такому випадку «зелений» перехід галузі оплачуватимуть кінцеві споживачі.