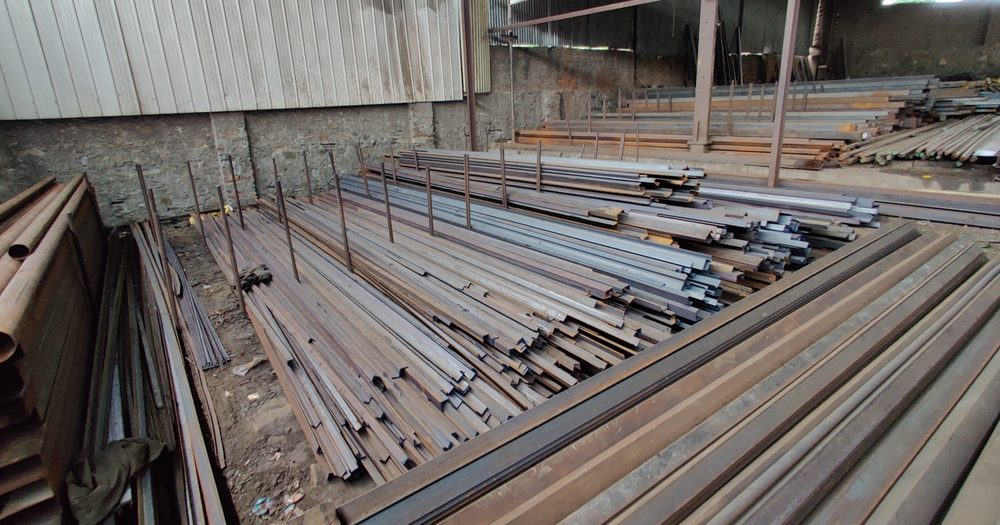
Статьи Глобальный рынок Индия 165 07 июля 2025
Правительство страны начало трансформацию с создания нормативно-правовой базы
Индийская металлургия сегодня самая перспективная в мире в контексте «зеленого» перехода. По темпам прироста стальной выплавки Индия с большим отрывом лидирует среди топ-10 крупнейших стран-производителей. И это несмотря на скромные объемы экспорта и все еще значительный импорт готовой стали. Сильный внутренний спрос пятой по величине экономики мира вот уже который месяц удерживает от снижения глобальный показатель металлопотребления.
При этом на 1 т стали в Индии приходится 2,54 т выбросов СО2 при среднемировом показателе 1,91 т. Т.е. потенциал для их снижения колоссальный. И в одном очень важном аспекте индийцы уже опережают остальных. Впервые в мире их сталь получила экологическую классификацию на государственном уровне. Тем самым создана нормативная база для предстоящего «зеленого» перехода.
Шаг первый: регламентация
Министерство стали Индии (MSI) 21 марта 2025 г. опубликовало Таксономию «зеленой» стали. Она вступит в силу в 2026-2027 ФГ и устанавливает 3 категории рейтинга. Для его присвоения сталь, выпускаемая предприятием, должна отвечать следующим критериям:
- 5* – при производстве 1 т готовой стали выбросы должны быть менее 1,6 т СО2;
- 4* – при выбросах 1,6-2,0 т СО2;
- 3* – при выбросах 2,0-2,2 т СО2;
При суммарной оценке категорий, Scope 1 и Scope 2 учитываются в полном объеме, Scope 3 – частично. В этот раздел включены выбросы СО2 при производстве кокса, агломерации и спекании железной руды, производстве окатышей и транспортировке сырьевых компонентов.
Присвоением рейтингов и выдачей соответствующих сертификатов будет заниматься National Institute of Secondary Steel Technology (NISST). Критерии рейтинга подлежат пересмотру раз в 3 года. Создание и ведение государственного реестра «зеленой» стали на основе выводов NISST поручено Бюро энергоэффективности (ВЕЕ).
Власти намерены отдавать предпочтение такой стали в рамках Политики «зеленых» государственных закупок (GPP), разработанной MSI. Это важный стимул, с учетом значительной роли государства в общем металлопотреблении.
По данным MSI, в 2022-2023 финансовом году (ФГ) объем госзаказов метпродукции составил 25 млн т. К 2030-2031 ФГ он увеличится до 67-73 млн т.
Шаг второй: оптимизация
Нулевых выбросов СО2 в экономике, и, соответственно, в металлургии, Индия планирует достичь к 2070 г. Это очень долго, скажут скептики. Зато реалистично. По данным Министерства стали, цена вопроса для отрасли – $283 млрд. Это средства, необходимые только для существующих метпредприятий суммарной годовой мощностью 200 млн т. Без учета дополнительных затрат для новых заводов мощностью 300 млн т, которые планируется построить до 2047 г.
Но тут речь идет о конечной цели – полностью безэмиссионном производстве. По факту же индийская сталь должна стать «зеленой» намного раньше. И обойдется это «всего» в $13 млрд. В такую сумму оценивается внедрение улучшающих технологий. Прежде всего в плане энергоэффективности. Сейчас удельное энергопотребление индийских метзаводов на технологии BF-BOF составляет 6-6,5 ГКал на 1 т стали, на технологии DRI-EAF/IF – 7 ГКал при среднемировом показателе 4,5-5 ГКал.
Пути снижения министерство видит в цифровизации производственных процессов. Плюс переход к использованию энергии из возобновляемых источников (ВИЭ). Сейчас индийская стальная индустрия получает из ВИЭ лишь незначительную часть потребляемой электроэнергии.
К 2030-2031 финансовому году показатель должен достичь 43,33%. Только за счет этого удельные выбросы СО2 снизятся с нынешних 2,54 т до 2,35 т на 1 т стали. Как известно, энергия ВИЭ значительно дороже, чем при производстве на угольных электростанциях. Сделать ее более доступной предполагается за счет отказа от платы за передачу э/э.
Среди других направлений можно отметить повышение эффективности материалов для индийской металлургии. Сейчас она в основном использует низкосортную железную руду.
По подсчетам MSI, увеличение содержания Fe на 1% в ЖРС повышает производительность доменной печи на 2% и снижает потребление кокса на 1%. Это достигается за счет дополнительного обогащения или гранулирования железной руды.
Насколько эти планы реалистичны? ArcelorMittal Nippon Steel India намерена к 2026-2027 ФГ, т.е. в ближайшем будущем, довести степень соответствия своей метпродукции «зеленым» критериям до 70%. Уже сейчас показатель выбросов СО2 у компании 2,17 т на 1 т стали. К 2030 г. он должен снизиться до 1,8 т. Так что вполне.
Вместе с тем очевидно, что хотя категория 5* для индийской «зеленой» стали предполагает довольно высокие выбросы (в сравнении с США, мировым лидером стальной декарбонизации), они не достижимы для комбинатов с BF-BOF. Например, та же ArcelorMittal Nippon Steel India в 2030 г. не сможет получить 5* для всей продукции. Поэтому нужны последующие шаги.
Инструменты декарбонизации
В отличие от США, сделавших ставку на R-EAF scrap based и Евросоюза, выбравшего Н2-DRI-EAF, Индия в своей Дорожной карте «озеленения» стального сектора не определяет технологический путь для декарбонизации. Она открыта к использованию всех возможных вариантов. Такая гибкость, безусловно, является преимуществом стратегии Нью-Дели.
Сегодня на электродуговые печи приходится 30% индийских сталеплавильных мощностей. При этом их загрузка ниже, чем у комбинатов BF-BOF – 74% и 84% соответственно. Среди новых предприятий общей мощностью 258 млн т в год на стадиях от проектирования до реализации доля EAF составляет 13%, или 33,54 млн т. Здесь можно выделить строительство завода Tata Steel в Пенджабе производительностью 750 тыс. т стали в год. А также проект госкомпании SAIL по строительству завода с EAF мощностью 1,5 млн т стали до 2029 г.
К 2047 г. Министерство стали задекларировало намерения увеличить долю лома в производстве стали с 15% до 50%. Это потребует дополнительных поставок. Получить их планируется за счет импорта. При этом уже сейчас Индия – один из крупнейших мировых импортеров металлолома, 9,39 млн т по итогам 2024 г. Очевидно, в будущем показатель может удвоиться. Сейчас импорт закрывает примерно 25% потребности в этом ресурсе. Внутренний ломосбор порядка 25 млн т.
Вместе с тем MSI отмечает сложности с обеспечением будущего производства в условиях, когда все больше стран ограничивают или даже прямо запрещают экспорт лома. Поэтому Индия реализует стратегию увеличения внутреннего ломосбора. В ее рамках крупные сталелитейщики, такие как SAIL и Tata Steel, инвестируют значительные средства в собственную ломозаготовку.
Также у властей есть планы по созданию общенациональной электронной площадки по торговле металлоломом. Это должно способствовать «детенизации» индийской заготовительной отрасли. Кроме того, уже действует программа, предлагающая владельцам б/у авто стимулы для утилизации. И рассматривается возможность ограничения экспорта стального лома. Объемы которого, впрочем, невелики: 8175 контейнеров в 2023-2024 ФГ.
Еще одним вариантом является технология CCUS, предусматривающая улавливание, утилизацию и хранение CO2. В индийской металлургии есть несколько пилотных проектов по улавливанию СО2. Но сейчас они нерентабельны. Текущую стоимость улавливания MSI оценивает в $45–60/т. Для метзаводов приемлемая цена менее $20/т. А утилизация и хранение тянут еще на $300-500/т. В таком случае готовая сталь подорожает на 100%. Поэтому ведется поиск технологических решений, способных сделать CCUS более доступной.
Как известно, Индия – мировой лидер по производству DRI. Но только 5% обжиговых печей работают на природном газе. Остальные – на угле. Поэтому еще одним направлением снижения выбросов является газификация этого производства. Таким путем пошла Jindal Steel. Компания построила установку газификации угля на заводе в штате Одиша. Получаемый синтетический газ используется для восстановления железа в окатышах до 99,99%.
В целом правительство ставит задачу достичь годового объемов газификации угля 100 млн т к 2030 г. С этой целью госкомпания Coal India Ltd. (CIL) создала совместные предприятия с Bharat Heavy Electricals Ltd. и Gas Authority of India Ltd. (GAIL). Под соответствующие проекты выделяется госфинансирование в размере 3,61 млрд.
И еще остается водород. А именно замена кокса и угля на Н2 в печах для выплавки чугуна и производства DRI. Пока данное направление в пилотной стадии. Tata Steel в апреле 2023 г. провела успешный пробный впрыск водорода в доменную печь на комбинате в Джамшедпуре. А в феврале 2025 г., т.е. спустя 2 года,компания сообщила о разработке труб из специальной стали, позволяющей транспортировать газообразный Н2 под высоким давлением.
Можно заметить, что работы продвигаются не слишком быстро. Но на самом деле Tata Steel и другим сталелитейщикам нет смысла форсировать технические изменения. Поскольку медленно развивается сама водородная индустрия.
Принятая в январе 2023 г. Национальная миссия «зеленого» водорода (NGHM) предусматривает выпуск 5 млн т продукта к 2030 г. Однако лишь в конце июня текущего года корпорация Adani Group смогла запустить первую в стране установку с мощностью электролизера 5 МВт в штате Гуджарат. В нынешнем году группа JSW такженамерена ввести в коммерческую эксплуатацию завод по производству Н2 с мощностью электролиза 25 МВт в штате Карнатака.
Таким образом, цель NGHM к 2030 г. точно не будет достигнута. Причина – слишком высокая себестоимость Н2. Сейчас она $4,6-6,3/кг, по данным Institute for Energy Economics&Financial Analysis. Правительство в нынешнем году отменило плату за передачу э/э, снизило тариф на распределение э/з и НДС для производителей «зеленого» водорода. За счет этих мер, по оценкам IEEFA, себестоимость уменьшается до $3-3,75/кг.
Но этого недостаточно. По данным Министерства стали, цена в пределах $1/кг сделает коммерчески обоснованным использование Н2 индийскими метзаводами. В таком случае они смогут потреблять порядка 1,1 млн т в год. Поэтому, очевидно, правительству придется искать дополнительные механизмы снижения стоимости производства «зеленого» водорода.
В целом расчеты MS показывают реалистичность декарбонизации индийской металлургии. С «зеленой» премией 30% к цене обычной продукции, с заменой 20% производства BF-BOF на безэмиссионное – «зеленая» сталь увеличит стоимость инфраструктурных проектов всего на 1,1%, выпуска авто и бытовой техники – на 0,5-1%. В таком случае «зеленый» переход отрасли будет оплачен за счет конечных потребителей.